راکتور هیدروترمال (اتوکلاو تفلنی)
راکتور هیدروترمال ، یکی از بهترین و ارزان ترین تجهیزات آزمایشگاهی است که زمانی که در سنتز مواد به بن بست می خوریم از آن استفاده میکنیم. “هیدروترمال” یک فناوری پیشرفته و کاربردی برای گسترهی وسیعی از صنایع شیمیایی است. این فرآیند دارای ریشه زمین شناختی است و شرایط حاکم بر سطوح درونی پوسته زمین را جهت اهداف صنعتی شبیهسازی و کنترل مینماید. فناوری هیدروترمال میتواند در زمینه سنتز، رشد، دگرگونی و تبدیل مواد شیمیایی کاربرد داشته باشد. همچنین بسیاری از فرآیندهای دهیدراسیون، تخریب شیمیایی، استخراج و فرآیندهای سونوشیمیایی، مکانوشیمیایی و الکتروشیمیایی، زینترینگ و غیره میتوانند تحت این فرایند انجام شوند. امروزه بیش از ۹۰ میلیون تن سنگ معدن بوکسیت (حاوی نمکهای آلومنیوم) با بهرهگیری از این فناوری مورد استخراج قرار میگیرد.
راکتو هیدروترمال تقریباً میتوانند در سنتز تمامی ترکیبات معدنی با ساختارهای عنصری، اکسید، سیلیکات، ژرمانات، فسفات، کلکوژناید، نیترید، کربنات و غیره بکار گرفته شود. در زمینه سنتز مواد پیشرفته، بزرگترین ترکیبات تک بلوری کوارتز (Single-Crystalline Quartz) و زئولیت (Zeolite) تاکنون بصورت مصنوعی با تکنولوژی هیدروترمال ساخته شدهاند. روش هیدروترمال میتواند برای سنتز مواد کاربردی نظیر مواد مغناطیسی، اپتیکی پیزوالکتریک، سرامیک و غیره در مقیاس بالا (تجاری) به صورت تک بلوری و چند بلوری (Poly-Crystalline) به کار گرفته شود. تک بلورهای ایجاد شده با این روش بسیار خالص و بزرگ هستند. پودرهای تهیه شده با فرآیند هیدروترمال دارای مزایایی همچون: ذرات مجزا، خلوص بسیار بالا (فاقد آلودگی)، غیرکلوخهای، با مورفولوژی و ترکیب بلوری مشخص (معمولاً تک بلوری) و بصورت تک پخش (Monodisperse) میباشند و به راحتی در حلال بازپخش می شوند.
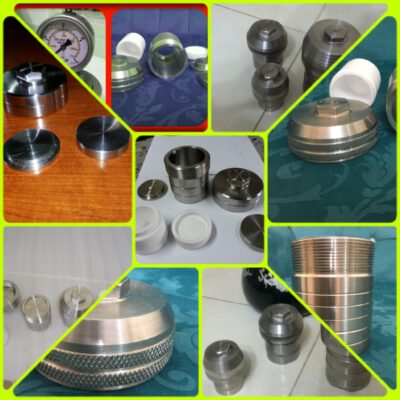
با توجه به طیف گسترده ای از واکنش هایی که در راکتور های آزمایشگاهی انجام می شوند مانند سنتز انواع نانو مواد ، نانو سرامیک ، گرافن ، زئولیت ، مزوپور و ترکیبات کئوردیناسیونی ، سنسور ها و نانو سنسورها ، بیومواد و شیمی پلیمر معدنی و … و عدم وجود و تولید اینگونه راکتور ها در کشور و هزینه بالای وارد کردن این محصول عملا باعث کاهش سرعت رشد در زمینه های تحقیقاتی مذکور و بسیاری از زمینه ای تحقیقاتی روز دنیا در کشور شده است . بنابراین این شرکت سعی کرده تا انواع راکتور های آزمایشگاهی مخصوصا راکتور های هیدروترمال را طراحی و از بهترین مواد در ساخت آن استفاده نماید تا از نظر کارایی و کیفیت چیزی کمتر از نمونه خارجی نداشته باشد و پس از آزمایشات متعدد توانسته با موفقیت طراحی و ساخت اولین راکتور را با موفقیت به پایان برساند . این راکتور ها باید درای یک شل بیرونی از جنس فلزی باشند که چند ویژگی مهم داشته باشد که عبارت اند از : مقاوم بودن به مواد شیمیایی ، اسید ها ، باز ها ، اکسیژن و آب و … ، عدم خاصیت مغناطیسی برای برخی از واکنش های خاص ، قابلیت تحمل فشار بالا ،قابلیت تحمل دماهای بالا، ظریب انبساط پایین و … و همچنین دارای یک شل درونی از جنس تفلون یا پلیمری خاص باشند که علاوه بر عدم واکنش باید تحمل دماها و فشار های بالا را داشته باشد . پس از مطالعات توانستیم بهترین جنس را برای شل بیرونی و شل درونی انتخاب نماییم و راکتور را طوری طراحی کنیم که مشابه جدید ترین راکتور نمونه خارجی بوده ولی با کارایی بیشتر و دارای برخی از نواقص نمونه های خارجی نمی باشد .انتخاب نوع فلز و تفلون با توجه به مطالعات SEM انواع فلزات و تفلون ها در محیط های RFNA و سایر اسید ها موادخوردنده و باز ها و … و میزان انبساط دمایی ، تحمل فشار و حرارت طی آزمایشات گوناگون متخصصین شرکت ، صورت گرفته است. پس از انتخاب مواد اولیه و طراحی قطعه با استفاده از دستگاه های CNC و فرز با دقت بالا این راکتور ها تراش داده می شوند .
راکتور هیدرورترمال و سولوترمال در شیمی کاتالیست ، کریستال ، پلیمر ، نانو ، کئوردیناسیون ، الکتروشیمی و همچنین در سنتز های بیوشیمی و سایر واکنش ها مورد استفاده قرار می گیرد. راکتور های هیدروترمال برای سنتز های شیمیایی تحت فشار و دمای معین نیز مورد استفاده قرار میگیرد. راکتور هیدروترمال در مهندسی محیط ، مهندسی انرژی ، مهندسی مواد و همچنین سایر رشته های علمی ، پژوهشی و آزمایشگاهی جهت پژوهش ، مطالعه و آموزش مورد استفاده قرار میگیرد.
ویژگی های راکتور هیدروترمال سکویا شیمی
- ساختار منطقی ، بدون مواد سازنده خطرناک ، بدون آلودگی با تضمین ایمنی
-
بدنه استیل ضد زنگ ، ضد اسید ، ضد خوردگی ، بدون خاصیت مغناطیسی
-
بدنه داخلی PTFE ، ضد زنگ ، ضد اسید ، ضد باز ، ضد مواد شیمیایی ، ضد خوردگی
-
طول عمر بسیار بالا ، قیمت پایین (یک سوم نمونه خارجی با همان کیفیت)
-
گارنتی ۱۲ ماهه محصولات از تاریخ خرید
پارامتر های راکتور هیدروترمال سکویا شیمی
دمای ایمنی : ۲۴۰ درجه سانتی گراد
فشار ایمنی : ۳ مگا پاسگال
سرعت سرد و گرم شدن : ۵ درجه سانتی گراد بر دقیقه
سایز : ۲۵ ، ۵۰ ، ۱۰۰ ، ۲۰۰میلی لیتر و …
نکات ایمنی راکتور هیدروترمال
۱- از حلال های انفجاری استفاده نشود.
۲- از حلال های با قابلیت اشتعال استفاده نشود.
۳- موادی که دارای قابلیت انفجار هستند یا ترکیبشان قابلیت انفجاری دارد نظیر N3 اجتناب شود.
۴- بهترین حلال آب است سعی شود از ان استفاده شود و در حد امکان حلال سمی استفاده نشود.
انتقال به صفحه خرید راکتور هیدروترمال
Hydrothermal reactor, Polymerization reactors, digestion tank, pressure vessel, experiment reflects the kettle.
Hydrothermal and solvothermal synthesis reactor is used in catalysis, crystal, polymer, Nano, Coordination, Electrochemical and Sensor Chemistry, also used in Biochemistry synthesis and other experiments.
Hydrothermal synthesis reactor is used to make new synthetic chemicals under a certain temperature and pressure. It is widely used in new materials, energy, environmental engineering and other fields of scientific research and experiments, it is a small commonly used reactor used in teaching and scientific research.
- Reasonable structure, non-spill of hazardous substances, pollution reduction, safety guarantee.
- Hydrothermal synthesis reactor using high quality Cr-Ni-Ti nonmagnetic stainless steel and refined processing.
- Lining uses complete PTFE material, it has the excellent acid resistance and alkali resistance.
- Stainless still shell, special PTFE liner, good corrosion resistance.
(۱) Safe Temp: ≤۲۴۰°C
(۲) Safe Pressure: ≤۳MPa
(۳) Heating and Cooling Rate: ≤۵°C/min
(۴) Specification: 25ml 50ml 100ml 150ml 200ml
we can offer customized size according to user’s needs.
فهرست مطالب مقاله کامل راکتور هیدروترمال (hydrothermal reactor)
۱- فصل اول : مقدمه ۸
۱-۱-۱ نکات ایمنی راکتور هیدروترمال ۱۰
۲- فصل دوم : مروری بر منابع ۱۲
۲-۱ رآکتور شیمیایی ۱۲
۲-۱-۱ مفاهیم واکنشهای شیمیایی ۱۳
۲-۱-۲ سینتیک واکنش ۱۳
۲-۱-۳ ترمودینامیک واکنش ۱۴
۲-۱-۴ اثر کاتالیزورها و بازدارندهها بر واکنش ۱۵
۲-۱-۵ کاتالیزورها انواع واکنشها ۱۶
۲-۱-۶ مفاهیم بنیادی راکتورها ۱۷
۲-۱-۷ معادله رآکتور ۱۸
۲-۱-۸ زمان اقامت، زمان نیمهعمر و زمان پایان واکنش ۱۸
۲-۱-۹ انتقال حرارت در رآکتور ۲۰
۲-۱-۱۰ میکسینگ و انتقال جرم در رآکتور ۲۱
۲-۱-۱۱ انواع راکتورهای شیمیایی ۲۲
۲-۱-۱۲ انواع رآکتور ازنظر فازهای درگیر در واکنش ۲۲
۲-۱-۱۳ رآکتور بسته و نیمه بسته ۲۴
۲-۱-۱۴ رآکتورهای پیوسته ۲۶
۲-۱-۱۵ رآکتور پلاگ ۲۷
۲-۱-۱۶رآکتورهای مخزنی باهمزن ۲۸
۲-۱-۱۷ رآکتورهای ثابت بستر و سیال بستر ۲۹
۲-۲ سنتز و پایداری نانوذرات مغناطیسی ۳۰
۲-۲-۱ مقدمه ۳۰
۲-۳ سنتز نانوذرات مغناطیسی ۳۱
۲-۳-۱ سنتز در فاز مایع ۳۱
۲-۳-۲ هم رسوبی (Co-precipitation) 32
۲-۳-۳ میکرو امولسیون (Microemulsion) 34
۲-۳-۴ تجزیه حرارتی (Thermal Decomposition) 35
۲-۳-۵ روشهای دیگر ۳۶
۲-۳-۶ سنتز در فاز گاز ۳۶
۲-۳-۷ سنتز در فاز جامد ۳۸
۲-۴روشهای محافظت (Protection Methods) 38
۲-۴-۱ قرار دادن پوشانندههای آلی هایا معدنی بر روی سطح نانوذرات مغناطیسی. ۳۹
۲-۴-۲ پوششهای معدنی (Inorganic Coatings) 40
۲-۵ عاملدار کردن نانوذرات مغناطیسی (Functionalization of Magnetic Nanoparticles) 41
۲-۵-۱ نتیجه گیری ۴۱
۲-۶ فرایند هیدروترمال برای تولید مواد؛ گذشته، حال و آینده ۴۲
۲-۶-۱ مقدمه ۴۲
۲-۶-۲ روندهای رایج در فناوری هیدروترمال ۴۴
۲-۶-۳ مفاهیم جدید در فناوری هیدروترمال ۴۵
۲-۶-۴ فراورش هیدروترمال ذرات ریز ۴۸
۲-۶-۵ فناوری هیدروترمال برای فناوری نانو ۵۰
۲-۶-۶ روندهای آینده تحقیقات هیدروترمال ۵۲
۲-۶-۷ نتیجه گیری ۵۳
۲-۷ واکنشهای سولوترمال: مسیری اصلی برای سنتز مواد جدید ۵۴
۲-۷-۱ مقدمه ۵۵
۲-۷-۲ شاخصهای اصلی حاکم بر واکنشهای سولوترمال ۵۶
۲-۷-۳ شاخصهای تومودینامیکی ۶۰
۲-۷-۴ انواع واکنشهای درگیر در فوایند سولوترمال ۶۰
۲-۷-۵ کاربردهای اصلی فرایند سولوتومال ۶۱
۲-۷-۶ توسعه فرایندهای جدید در تهیه نانوبلورهای عاملی ۶۱
۲-۷-۷ نتیجه گیری ۶۲
۲-۸ کنترلر دما ۶۳
۲-۸-۱ حسگر RTD : 63
۲-۸-۲ ترموکوپل: ۶۴
۲-۸-۳ انواع کنترلر دما ۶۴
۲-۸-۴ انواع کنترلر ازنظر ظاهر ۶۴
۲-۸-۵ کنترل کننده PID Controller” PID”: 65
۲-۸-۶ انواع خروجی کنترلر( ترموستات): ۶۶
۲-۸-۷ کاربرد کنترلر(ترموستات): ۶۷
۲-۹ مواد پیزوالکتریک ۶۷
۲-۹-۱ تعریف و تاریخچه ۶۸
۲-۹-۲ فرآیند تولید سرامیک های پیزوالکتریک ۷۰
۲-۹-۳ روابط ساختاری و خواص مواد ۷۳
۲-۹-۴ کاربرد مواد پیزوالکتریک ۷۴
۳- فصل سوم : نحوه ساخت و طراحی ۷۵
۳-۱ مزیت های راکتور طراحی شده : ۸۳
۳-۲ مزیت نسبت به نمونه خارجی ۸۳
۳-۳ مشخصات راکتور تولیدی ۸۴
۳-۴ مواد مورد نیاز برای تولید راکتور ۱۰۰ سی سی ۱۰۰
۳-۵ ابعاد راکتور هیدروترمال تولیدشده ۱۰۱
۳-۶ محصول نهایی ۱۰۷
۳-۷ نحوه سنتز پودر پیزوالکتریک PZT به روش هیدروترمال ۱۱۳
مقدمه ۱۱۳
۳-۷-۱ شرایط ونحوه انجام آزمایش سنتز ۱۱۳
۴- فصل چهارم : نتیجه گیری ۱۱۵
۴-۱ نتایج کلی ۱۱۸
۵ مراجع ۱۱۹
فهرست اشکال
شکل ۲‑۱: طرحی از یک فرایند کاتالیزوری سیال بستر. در سمت راست رآکتور شیمیایی و در سمت چپ واحد بازیابی کاتالیست قرار دارد ۱۵
شکل ۲‑۲: یک راکتور شیمیایی در ابعاد بزرگ برای تولید صنعتی ۱۷
شکل ۲‑۳: یک رآکتور شیمیایی در ابعاد کوچک جهت تحقیقات آزمایشگاهی ۱۷
شکل ۲‑۴: تصویر شماتیک یک رآکتور به همراه کویلهای گرمایشی و سرمایشی در اطراف آن ۲۰
شکل ۲‑۵: برشی از یک رآکتور مخزنی به همراه سیستم خنککننده جاکتی که شفت و پروانه همزن در وسط آن دیده میشود ۲۱
شکل ۲‑۶:: نماد رآکتور بسته ۲۴
شکل ۲‑۷: : نماد رآکتور سی اس تی آر ۲۶
شکل ۲‑۸: طرح شماتیک از مقطع فرضی یک رآکتور پلاگ ۲۷
شکل ۲‑۹: داخل یک نوع رآکتور سی اس تی آر که در آن همزن و شفت آن به همراه بافلها (پایین تصویر) دیده میشوند ۲۸
شکل ۲‑۱۰ : نمودار LaMer 32
شکل ۲‑۱۱: شماتیک سنتز نانوذرات مغناطیسی Fe۳O۴ با استفاده از روش هم رسوبی؛ ابتدا محلولی از یونهای آهن در اسیدکلریدریک تهیهشده و سپس این محلول بر روی محلولی از دی ایزوپروپیل آمین (DIPA) ریخته میشود که نتیجه آن ایجاد رسوبی از نانوذرات اکسید آهن خواهد بود. ۳۳
شکل ۲‑۱۲: شماتیکی از مایسل نرمال و معکوس ۳۵
شکل ۲‑۱۳: برخی از پوشش های آلی مورداستفاده جهت تضمین پایداری نانوذرات مغناطیسی ۳۹
شکل ۲‑۱۴: تصویر TEM از نانوذرات مغناطیسی پوشیده شده با سیلیکا ۴۰
شکل ۲‑۱۵ : انرژی در مقایسه با کارایی / تنوع در فرایندهای زیستی و دست ساز بشر ۴۷
شکل ۲‑۱۶: شماتیک مقایسه تولید تکمرحلهای و چند مرحلهای مواد پیشرفته ۴۷
شکل ۲‑۱۷: نقشهای مایع هیدروترمال بر روی نمونه جامد حلال میتواند بهعنوان جاذب، واکنشگر و یا حلال عمل کند ۴۸
شکل ۲‑۱۸: مقایسه تولید مواد با روش هیدروترمال با سایر روشهای مرسوم ۵۰
شکل ۲‑۱۹: . نانوساختارهای کربن بهدستآمده از واپاشی کاربید فلزات تحت شرایط هیدروترمال فوق بحرانی ۵۲
شکل ۲‑۲۰: ساختارهای گل مانند اکسید روی. الف) عکس با بزرگ نمایی پایین؛ ب) خوشه گلهای ZnOج) گلهایی با پدالهای چندگانه؛ د) گل مجزا با پدالهای تک لایه. ۵۸
شکل ۳‑۱ : راکتور هیدروترمال با بدنه استیل مقاوم تا دمای ۲۸۰ درجه سانتی پایه و شل داخلی PTFE 76
شکل ۳‑۲: کوره ی افقی جهت قرار گیری راکتورهای هیدروترمال بدون سیستم گرمایشی ۷۶
شکل ۳‑۳: سیستم کنترل دما همراه باهمزن مغناطیسی برای راکتورهای هیدروترمال ۷۷
شکل ۳‑۴: محفظه ضد انفجار برای راکتورهای هیدروترمال با فشار بالا ۷۸
شکل ۳‑۵: راکتور هیدروترمال دارای فشارسنج آنالوگ ۷۹
شکل ۳‑۶:راکتور هیدروترمال با سیستم کنترل دما و فشار و کوره مخصوص جهت گرامادهی ۸۰
شکل ۳‑۷:نمایی از راکتور هیدروترمال بدون شل داخلی PTFE 81
شکل ۳‑۸ : نمایی از راکتور هیدروترمال با شل داخلی ppp مقاوم تا ۳۵۰ درجه سانتی پایه ۸۲
شکل ۳‑۹: معرفی قسمت های مختلف از راکتور هیدروترمال ۸۲
شکل ۳‑۱۰: راکتور هیدرومال تولیدی با کنترل دما ۸۷
شکل ۳‑۱۱:معرفی قسمت های مختلف راکتورهای هیدروترمال دارای کنترل دما و فشار باقابلیت اتصال به کامیوتر ۸۸
شکل ۳‑۱۲: نمونه ای از راکتور هیدروترمال غیر استاندارد منفجر شده ۸۹
شکل ۳‑۱۳: نمونه ای از کوره ای که یک عدد راکتور هیدروترمال غیر استاندارد و بی کیفیت در آن منفجر شده است ۸۹
شکل ۳‑۱۴: تصویری از مواد اولیه استیل ۳۱۶ جه تولید راکتور هیدورترمال ۱۰۲
شکل ۳‑۱۵: نمای شماتیک از مراحل تولید راکتور هیدروترمال و ماشین کاری ۱۰۳
شکل ۳‑۱۶ : تصویر کنترلر مورداستفاده ۱۰۴
شکل ۳‑۱۷: شماتیکی از معرفی مدل کنترلر دما ۱۰۵
شکل ۳‑۱۸: ابعادکنترلر آتونیکس TC4S-24R 105
شکل ۳‑۱۹: مدار معادل کنترلر دما بر اساس نوع خروجی رله یاSSR 106
شکل ۳‑۲۰: تصاویری از راکتور تولیدشده ۱۱۳
شکل ۴‑۱: الگوی پراش اشعه x پودر سنتز شده در سه زمان مختلف ۱،۳،۲۴ ساعت ۱۱۷
شکل ۴‑۲: تصویر میکروسکوپ الکترونی روبشی(SEM) از پودر PZT سنتز شده در ۱۵۰ درجه سانتیگراد وبه مدت ۳ساعت ۱۱۸
فهرست جداول
جدول ۲‑۱: انواع راکتورهای شیمیایی ازنظر فازهای درگیر در واکنش ۲۲
جدول ۲‑۲: پیشرفت هیدروترمال تولید مواد پیشرفته ۴۵
جدول ۲‑۳: مقایسه روشهای سنتز پودرهای گوناگون ۴۹
جدول ۲‑۴: شاخصهای کلیدی موثر در واکنشهای سولوترمال ۵۶
جدول ۳‑۱: جدول مقاومت انواع پیشماده ها جهت ساخت راکتور نسبت به مواد شیمایی مختلف ۹۰
۱- فصل اول : مقدمه
راکتور هیدروترمال ، یکی از بهترین و ارزانترین تجهیزات آزمایشگاهی است که زمانی که در سنتز مواد به بنبست میخوریم از آن استفاده میکنیم. “هیدروترمال” یک فناوری پیشرفته و کاربردی برای گسترهی وسیعی از صنایع شیمیایی است. این فرآیند دارای ریشه زمینشناختی است و شرایط حاکم بر سطوح درونی پوسته زمین را جهت اهداف صنعتی شبیهسازی و کنترل مینماید. فناوری هیدروترمال میتواند درزمینهٔ سنتز، رشد، دگرگونی و تبدیل مواد شیمیایی کاربرد داشته باشد. همچنین بسیاری از فرآیندهای دهیدراسیون، تخریب شیمیایی، استخراج و فرآیندهای سونوشیمیایی، مکانوشیمیایی و الکتروشیمیایی، زینترینگ و غیره میتوانند تحت این فرایند انجام شوند. امروزه بیش از ۹۰ میلیون تن سنگ معدن بوکسیت (حاوی نمکهای آلومینیوم) با بهرهگیری از این فناوری مورد استخراج قرار میگیرد.[۱]
سنتز هیدروترمال روشی است که بهطور گسترده برای تولید پودرهای کوچک و ذرات در درجه حرارت بالا، اغلب بالاتر از نقطهجوش مایع، استفاده میشود.. در چند سال اخیر گروههای تحقیقاتی زیادی یا شرکتهای متعددی تولید نانولولههای کربنی را بهوسیله این روش گزارش کردهاند[۲-۵].
این روش بر اساس حرارت دادن واکنشگرها، اغلب نمکهای فلزی، اکسید، هیدروکسید یا پودر فلز بهعنوان محلول یا سوسپانسیون درون مایع (معمولاً نه لزوماً آب) در دما و فشار بالا ، تا حدود ۳۰۰ درجهی سانتی گراد و حدود MPa۱۰۰ (۱۰۰ برابر فشار سطح دریا) میباشد. هسته گذاری و رشد ذرات تحت این شرایط اتفاق میافتد که باعث ایجاد نانو اکسیدها ، ذرات فلزی یا غیر اکسیدی با شکل و اندازهی کنترلشده میشود.
در این روش، بهطور مستقیم پودرها و ذرات در مقیاس نانو یا زیر میکرو (شامل نانولولههای کربنی و کوانتوم داتهای کلوئیدی) تولید میشود و همچنین بهوسیلهی کاهش آلودگی و دمای کم سنتز مشخصه سازی میشود.
در سنتز هیدروترمال، تبدیل مواد تحت دما و فشار بالا اتفاق میافتد. این روش عمدتاً برای تولید نانو پودرهای با کیفیت بالا استفاده میشود[۶-۸].
راکتور هیدروترمال تقریباً میتوانند در سنتز تمامی ترکیبات معدنی با ساختارهای عنصری، اکسید، سیلیکات، ژرمانات، فسفات، کلکوژناید، نیترید، کربنات و غیره بکار گرفته شود. درزمینهٔ سنتز مواد پیشرفته، بزرگترین ترکیبات تک بلوری کوارتز [۹](Single-Crystalline Quartz) و زئولیت[۱۰] (Zeolite) تاکنون بهصورت مصنوعی با فنّاوری هیدروترمال ساختهشدهاند. روش هیدروترمال میتواند برای سنتز مواد کاربردی نظیر مواد مغناطیسی، اپتیکی پیزوالکتریک، سرامیک و غیره در مقیاس بالا (تجاری) بهصورت تک بلوری و چند بلوری (Poly-Crystalline) به کار گرفته شود. تکبلورهای ایجادشده با این روش بسیار خالص و بزرگ هستند. پودرهای تهیهشده با فرآیند هیدروترمال دارای مزایایی همچون: ذرات مجزا، خلوص بسیار بالا (فاقد آلودگی)، غیر کلوخهای، با مورفولوژی و ترکیب بلوری مشخص (معمولاً تک بلوری) و بهصورت تکپخش (Monodisperse) میباشند و بهراحتی در حلال بازپخش میشوند.
با توجه به طیف گستردهای از واکنشهایی که در راکتورهای آزمایشگاهی انجام میشوند مانند سنتز انواع نانومواد ، نانو سرامیک ، گرافن ، زئولیت ، مزوپور و ترکیبات کئوردیناسیون ، حسگرها و نانو حسگرها ، بیو مواد و شیمی پلیمر معدنی و … و عدم وجود و تولید اینگونه راکتورها در کشور و هزینه بالای واردکردن این محصول عملاً باعث کاهش سرعت رشد درزمینهٔ های تحقیقاتی مذکور و بسیاری از زمینهای تحقیقاتی روز دنیا در کشور شده است . بنابراین ما سعی کردهایم تا ا راکتورهای هیدروترمال را طراحی و از بهترین مواد در ساخت آن استفاده نماییم تا ازنظر کارایی و کیفیت چیزی کمتر از نمونه خارجی نداشته باشد و پس از آزمایشها متعدد توانسته با موفقیت طراحی و ساخت اولین راکتور را با موفقیت به پایان برساند . این راکتورها باید دارای یک شل بیرونی از جنس فلزی باشند که چند ویژگی مهم داشته باشد که عبارتاند از : مقاوم بودن به مواد شیمیایی ، اسیدها ، بازها ، اکسیژن و آب و … ، عدم خاصیت مغناطیسی برای برخی از واکنشهای خاص ، قابلیت تحمل فشار بالا ،قابلیت تحمل دماهای بالا، ضریب انبساط پایین و … و همچنین دارای یک شل درونی از جنس تفلون یا پلیمری خاص باشند که علاوه بر عدم واکنش باید تحمل دماها و فشارهای بالا را داشته باشد . پس از مطالعات توانستیم بهترین جنس را برای شل بیرونی و شل درونی انتخاب نماییم و راکتور را طوری طراحی کنیم که مشابه جدیدترین راکتور نمونه خارجی بوده ولی با کارایی بیشتر و دارای برخی از نواقص نمونههای خارجی نیست .انتخاب نوع فلز و تفلون با توجه به مطالعات SEM انواع فلزات و تفلونها در محیطهای RFNA و سایر اسیدها موادخوردنده و بازها و … و میزان انبساط دمایی ، تحمل فشار و حرارت طی آزمایشها گوناگون متخصصین شرکت ، صورت گرفته است. پس از انتخاب مواد اولیه و طراحی قطعه با استفاده از دستگاههای CNC و فرز با دقت بالا این راکتورها تراش داده میشوند .
راکتور هیدروترمال و سولوترمال در شیمی کاتالیست ، کریستال ، پلیمر ، نانو ، کئوردیناسیون ، الکتروشیمی و همچنین در سنتزهای بیوشیمی و سایر واکنشها مورداستفاده قرار میگیرد. راکتورهای هیدروترمال برای سنتزهای شیمیایی تحتفشار و دمای معین نیز مورداستفاده قرار میگیرد. راکتور هیدروترمال در مهندسی محیط ، مهندسی انرژی ، مهندسی مواد و همچنین سایر رشتههای علمی ، پژوهشی و آزمایشگاهی جهت پژوهش ، مطالعه و آموزش مورداستفاده قرار میگیرد.
نکات ایمنی راکتور هیدروترمال
۱- از حلالهای انفجاری استفاده نشود.
۲- از حلالهای باقابلیت اشتعال استفاده نشود.
۳- موادی که دارای قابلیت انفجار هستند یا ترکیبشان قابلیت انفجاری دارد نظیر N3 اجتناب شود.
۴- بهترین حلال آب است سعی شود از آن استفاده شود و در حد امکان حلال سمی استفاده نشود.
۲- فصل دوم : مروری بر منابع
رآکتور شیمیایی
رآکتور شیمیایی یا واکنشگاه شیمیایی وسیلهای است که در آن واکنشهای شیمیایی انجام میشود و طی آن مواد اولیه خام به محصولات تبدیل میشوند.
طراحی و بهرهبرداری از رآکتورهای شیمیایی ازجمله مهمترین وظایف متخصصین صنایع شیمیایی ازجمله مهندسین شیمی است. طراحی رآکتور شیمیایی نیازمند شناخت درست از واکنش شیمیایی انجامگرفته در رآکتور است و برای این منظور تسلط بر علومی چون ترمودینامیک شیمیایی،سینتیک شیمیایی و ریاضیات ضروری است.
رآکتورهای شیمیایی میتوانند در ابعاد بزرگ و برای مصارف صنعتی یا در ابعاد کوچک جهت کاربردهای آزمایشگاهی و تحقیقاتی ساخته و تولید شوند. همچنین جنبههای اقتصادی نیز بر طراحی بهینهٔ رآکتور تأثیرگذار است. ازجمله صرف هزینهٔ کمتر برای طراحی رآکتور کاراتر و کوچکتر، صرف انرژی کمتر برای تولید محصول بیشتر، رساندن مواد اولیه به بیشترین درصد تبدیل و بالا بردن راندمان فرایند و … .
در طراحی رآکتورها پارامترهای زیادی ازجمله:زمان اقامت( )، حجم(V)، دما(T)، فشار(P)، غلظت گونههای شیمیایی(C۱,C۲,C۳,… ,Cn)، ضریب انتقال حرارت (U, h)، سرعت واکنش (r) و … ، دخالت دارند. رآکتورهای شیمیاییبر اساس نوع واکنش و موارد کاربرد در اشکال مختلف و با جزئیات خاص طراحی میشوند که پیچیدگی آنها را زیاد میکند. اما میتوان رآکتورها را در چند دستهٔ بزرگ و کلی ازجمله رآکتورهای پیوسته و ناپیوسته، رآکتورها سیال بستر یا ثابت بستر، رآکتورهای لولهای و مخزنی یا رآکتورهای همگن و ناهمگن، طبقهبندی کرد. رفتار رآکتورها معمولاً با معادلاتی موسوم به معادلهٔ رآکتور مطرح میشود که برای گونههای مختلف رآکتور متفاوت بوده و رابطهٔ ریاضیاتی بین پارامترهای مؤثر در رآکتور را بیان میکند.
مفاهیم واکنشهای شیمیایی
واکنش شیمیایی فرآیندی است که طی آنیک یا چند ماده به مواد دیگر تبدیل میشوند. مواد اولیه موادی با ارزش اقتصادی کمتر میباشند و در عوض محصولات موادی با ارزش بالاتر است. درک سینتیک و سازوکار واکنش یکی از نکات مهم در طراحی رآکتورهای صنعتی است. معادله سرعت، تعادلی بودن یا نبودن، فاز مواد درگیر در واکنش (جامد، مایع، گاز)، گرماگیر یا گرماده بودن و همچنین اثر کاتالیزور بر واکنش، ازجمله مهمترین نکاتی است که در طراحی رآکتور حائز اهمیت است
سینتیک واکنش
سینتیک واکنش شیمیایی عبارت است از بررسی سازوکار انجام یک واکنش شیمیایی. علم سینتیک شیمیایی بهطور کامل به نحوه انجام واکنش، واکنشهای جانبی، مواد واسط تولیدی و بسیاری از جزئیات یک واکنش میپردازد. سرعت واکنش و بستگی آن به غلظت گونههای درگیر در واکنش با استفاده از رابطهای به نام معادله سرعت بیان میشود. بهطورکلی تغییر غلظت گونهای موجود در واکنش در واحد زمان را سرعت واکنش نسبت به آن ماده تعریف میکنند مثلاً برای واکنش ساده A → B معادله سرعت بهصورت زیر است:
معادله سرعت واکنش را میتوان به شکل زیر هم بازنویسی کرد. باید توجه داشت که در معادله زیر علامت منفی بهطور قراردادی نشاندهنده مصرف گونه است. به همین ترتیب برای تولید گونه از علامت مثبت استفاده میشود.
در این معادله عددی ثابت است که به «ثابت سرعت واکنش» معروف است و عدد بزرگتر نشاندهنده واکنش سریعتر است. همچنین میزان بستگی سرعت واکنش به غلظت را نشان میدهد که به درجه واکنش نسبت به گونه معروف است. این پارامتر معمولاً عددی بین صفر تا ۳ است. همچنین اگر گونههای واکنشدهنده بیش از یکی باشد، از جمع توانهای واکنشدهندهها، درجه کلی واکنش حاصل میشود. روشهای گوناگونی برای به دست آوردن این معادلات وجود دارد؛ اعم از روشهای تئوری یا استفاده از دادههای آزمایشگاهی.
ترمودینامیک واکنش
بررسی واکنشها ازنظر انرژی، در حوزه مباحث ترمودینامیک شیمیایی است. گرماگیر یا گرماده بودن واکنش و میزان انرژی تبادل شده در واکنش از نکات مهم در این علم است. اهمیت این مسئله ازآنجهت است که برای رآکتورها میباید دستگاههای گرمایش یا سرمایش طراحی شود تا تبادل انرژی بهخوبی انجام شود. وجود هر نوع اشکال یا محاسبات نادرست در سیستم تبادل انرژی موجب اخلال در انجام واکنش، کیفیت محصول، مقدار محصول و حتی خطر جانی و مالی میشود. بهعنوان نمونه در واکنشهای گرماده شدید، درصورتیکه گرمای تولیدشده در واکنش بهخوبی تبادل نشود، افزایش بیرویه دما داخل رآکتور میتواند منجر به افزایش حجم و بالا رفتن فشار شود، همچنین در واکنشهایی که با تولید گاز شدید انجام میشوند، ممکن است موجب انفجار شود[۱۱].
اثر کاتالیزورها و بازدارندهها بر واکنش
شکل ۲‑۱: طرحی از یک فرایند کاتالیزوری سیال بستر. در سمت راست رآکتور شیمیایی و در سمت چپ واحد بازیابی کاتالیست قرار دارد
موادی هستند که با دخالت در واکنش و تغییر مسیر واکنش، سرعت واکنش را بالا میبرند. از کاتالیزورها در واکنشهایی که در شرایط معمول با سرعت پایین انجام میشوند استفاده میشود. در نقطه مقابل مواد دیگری به نام بازدارندهها وجود دارند که مانند کاتالیست هستند با این تفاوت که افزودن آن به واکنش موجب کندی و حتی توقف واکنش میشود. بازدارندهها بهطور ویژه در صنایع پلیمر و برای کنترل فرآیندهای پلیمراسیون در رآکتور شیمیایی کاربرد دارد. کاتالیزورها و بازدارندهها میتوانند بهصورت همگن با فاز مواد درگیر در واکنش مصرف شوند که به واکنشهای کاتالیستی همگن معروف هستند. واکنشهایی که کاتالیست و مواد درگیر در واکنش در یکفاز قرار ندارند به واکنشهای کاتالیستی ناهمگن معروف هستند.
این مواد معمولاً با درصد بسیار پایین و به اشکال مختلف در فرایند مورداستفاده قرار میگیرند. ممکن است کاتالیزور یا بازدارنده بهصورت ثابت در رآکتور شیمیایی قرار داشته باشد و مواد واکنشدهنده پس از تماس با آن خارج شوند. در نقطه مقابل ممکن است این مواد بهصورت پودر یا اشکال دیگر به داخل رآکتور تزریق و سپس از آن خارج شوند. بهعنوان نمونه در فرایند کراکینگ کاتالیزوری سیال بستر، کاتالیست زئولیت بهصورت پودر به داخل رآکتور تزریق میشود. پس از اشباع شدن کاتالیزور، همراه با فرآوردهها از فرایند خارج و پس از جداسازی و بازیابی مجدداً به داخل رآکتور تزریق میشود. بهاینترتیب این چرخه دائماً ادامه پیدا میکند و کاتالیزور در فرایند مرتباً در گردش است.
کاتالیزورها انواع واکنشها
توجه به ماهیت و نوع واکنش نیز در طراحی رآکتور از اهمیت بالایی برخوردار است. مثلاً در واکنشهای یکطرفه تقریباً تمام مواد واکنشدهنده با نسبتهای استوکیومتری مشخص مصرف میشوند. اما در واکنشهای تعادلی در یک سیستم بسته، در دما و فشار مشخص، مواد اولیه و مواد تولیدی پس از مدتی با یکدیگر به تعادل میرسند، یعنی باگذشت زمان، غلظت مواد دچار تغییر نشده و مقداری از مواد اولیه بهصورت واکنش نداده در سیستم باقی میماند. رفتار واکنشهای تعادلی با اصلی به نام اصل لوشاتلیه بررسی میشود.
در واکنشهای رقابتی یک یا چند واکنش جانبی، که منجر به تولید مواد بلااستفاده میشود، در کنار واکنش اصلی رخ میدهد. در این نوع واکنشها باید پارامترهای فرایند طوری طراحی شود که بیشترین مقدار ممکن از ماده مطلوب تولید شود.
همچنین در واکنشهای سری چند واکنش پشت سر هم انجام میشود تا محصول نهایی تولید شود. به عبارتی واکنش کلی از ترکیب چند واکنش به وجود میآید. در این نوع واکنشها، سرعت کلی واکنش بهسرعت کندترین واکنش بستگی دارد.
مفاهیم بنیادی راکتورها
شکل ۲‑۲: یک راکتور شیمیایی در ابعاد بزرگ برای تولید صنعتی
شکل ۲‑۳: یک رآکتور شیمیایی در ابعاد کوچک جهت تحقیقات آزمایشگاهی
رآکتورهای شیمیایی محلی برای انجام یک واکنش شیمیایی هستند. رآکتورها میتوانند جهت تولید انبوه مواد شیمیایی، دارویی و مواد پتروشیمی و در واحدهای صنعتی بزرگ به کار گرفته شوند یا جهت انجام مطالعات و تحقیقات و در ابعاد کوچک به کار بروند.
طراحی رآکتورها با توجه به مکانیسم واکنش و همچنین نوع واکنش و فاز مواد درگیر در واکنش متفاوت است. در طراحی رآکتورهای شیمیایی برخی از پارامترها مانند دما، فشار و دبی مواد ورودی و خروجی، توسط طراح قابلتغییر است. اما برخی پارامترها مانند ماهیت واکنش، گرماگیر یا گرماده بودن، ایجاد گاز یا تغییر در حجم مواد، ازجمله مواردی است که به طبیعت واکنش مربوط بوده و در اختیار طراح قرار ندارد. از مجموع این موارد میتوان نتیجه گرفت که رآکتورها در اشکال پیوسته یا بسته، بستر ثابت یا بستر متلاطم، تحتفشار یا در فشار اتمسفری یا با اثر کاتالیست یا بدون اثر کاتالیست طراحی میشوند. برخی از پارامترهایی که تقریباً در تمام راکتورها مطرح بوده و حائز اهمیت به جهت شناخت راکتور و عملکرد آن است، میتوان به موارد زیر اشاره کرد:
معادله رآکتور
معادله رآکتور رابطه ریاضیاتی است که پارامترهای مربوط به رآکتور مانند زمان اقامت و حجم رآکتور را بهسرعت واکنش، نشان میدهند. این معادلات میتوانند بهصورت عمومی برای دستهای خاصی رآکتورها مطرح شوند یا بهصورت تجربی برای گونه خاصی از رآکتور به دست بیایند.
زمان اقامت، زمان نیمهعمر و زمان پایان واکنش
در رآکتورهای پیوسته که بهطور مداوم مواد خام وارد و محصولات خارج میشوند، نمیتوان زمان مشخصی برای انجام واکنش و تبدیل مواد اولیه به محصول بیان کرد. درنتیجه از کمیتی به نام زمان اقامت استفاده میشود. زمان اقامت متوسط زمانی است که یکذره وارد رآکتور شده و تا زمان خروج در آنجا در حال واکنش است. این کمیت بهصورت زیر نشان داده میشود:
در این معادله، V نشاندهنده حجم رآکتور، q دبی حجمی ورودی و خروجی از رآکتور و زمان اقامت است. زمان اقامت یکی از پارامترهای مورداستفاده در معادله رآکتور است
زمان نیمهعمر مدتزمانی است که نیمی از غلظت ماده اولیه تزریقشده در رآکتور، به محصولات تبدیل میشوند. بهعنوانمثال در واکنش سادهA → B نیمهعمر واکنش بهصورت زیر تعریف میشود:
از این رابطه با در نظر گرفتن شرایط مرزی زیر انتگرال میگیریم:
همچنین زمان پایان واکنش به شیوه مشابه بهصورت زیر به دست میآید. باید توجه داشت که تنها واکنشهایی پایانپذیر هستند که در آنها باشد، در غیر این صورت همواره مقداری از مواد اولیه در رآکتور بهصورت واکنش نداده باقی میماند.
از این رابطه با در نظر گرفتن شرایط مرزی زیر انتگرال میگیریم:
انتقال حرارت در رآکتور
شکل ۲‑۴: تصویر شماتیک یک رآکتور به همراه کویلهای گرمایشی و سرمایشی در اطراف آن
فرایند چه ازنظر عملیاتی و چه ازنظر ایمنی از اهمیت بالایی برخوردار است. عمده واکنشهای شیمیایی یا گرماده هستند یا گرماگیر. درنتیجه در حین انجام واکنش ممکن است محتویات درون رآکتور گرم شده یا سرد شوند. بالا رفتن بیشازحد دما در رآکتور میتواند موجب اختلال در عملکرد رآکتور و تجهیزات کنترلی آن شود و از همه مهمتر، ریسک خطر انفجار و نشت مواد را بالا میبرد. همچنین درصورتیکه واکنش گرماگیر باشد، با پیشرفت واکنش محتویات رآکتور سردتر میشود و ممکن است موجب کندی سرعت واکنش یا انجماد در رآکتور و تجهیزات آن شود. درنتیجه میبایست در رآکتورها، همواره دما را در حد مناسب و ایمن نگه داشت. برای این منظور از مبدلها و تجهیزات انتقال حرارت استفاده میشود. یکی از متداولترین روشها برای کنترل دمای رآکتورها استفاده از جاکت یا کویلهای تبادل حرارت است. در جاکتها، یک لایه از سیال با دمای بالاتر یا پایینتر برای تنظیم دما، در اطراف رآکتور و بدون تماس جرمی با محتویات رآکتور، مرتباً در چرخش است. در روش کویل نیز لولههایی که حاوی سیال سردتر یا گرمتر است بهصورت مارپیچ یا اشکال دیگر در اطراف رآکتور قرار داده میشود تا تبادل حرارت با رآکتور انجام شود.
میکسینگ و انتقال جرم در رآکتور
شکل ۲‑۵: برشی از یک رآکتور مخزنی به همراه سیستم خنککننده جاکتی که شفت و پروانه همزن در وسط آن دیده میشود
فرایند هم زدن و انتقال جرم در رآکتورها از اهمیت بالایی برخوردار است زیرا درصورتیکه محتویات داخل رآکتور بهخوبی ترکیب نشوند، امکان واکنش ندادن بخشی از مواد و درنتیجه پایین آمدن کیفیت محصول میشود. عمل هم زدن در رآکتورهای مخزنی شکل، با استفاده از همزنهای دوار که به شفت و الکتروموتور متصل است انجام میشود. در رآکتورهای لولهای (پلاگ) نیز به دلیل شکل رآکتور، عمل اختلاط در طول لوله با حرکت سیال اتفاق میافتد. شکل، نحوه قرارگیری و سرعت چرخش همزن بستگی به عواملی چون، حجم مخزن، شکل مخزن، ویسکوزیته سیال و … دارد. همچنین انتخاب جنس همزن و بدنه رآکتور به مواد داخل رآکتور بستگی دارد. مثلاً اگر مواد داخل رآکتور خورنده باشند، استفاده از فولاد و موادی که امکان خورده شدن در آن وجود دارد، غیرمنطقی است. در اینگونه موارد انتخاب مواد جایگزین یا پوشش دهی تجهیزات با لعابهای سرامیکی یا پوششهای پلیمری روش مناسبی در جلوگیری از خوردگی و واکنشهای ناخواسته است.
انواع راکتورهای شیمیایی
رآکتورهای شیمیایی طراحیهای پیچیدهای دارند که گاه طی سالیان متمادی برای یک فرایند خاص به تکامل رسیده است. پارامترهای بسیار بر طراحی و شکل رآکتور مؤثر هستند که موجب تنوع انواع رآکتورها میشوند. اما میتوان بر اساس برخی پارامترهای اساسی، رآکتورها را به دستههای عمده تقسیم کرد که در زیر به آن میپردازیم.
انواع رآکتور ازنظر فازهای درگیر در واکنش
واکنشها در رآکتور ممکن است بهصورت همگن (تمامی مواد در یکفاز هستند) یا ناهمگن (مواد درگیر در واکنش در فازهای مختلف قرار دارند) انجام شود. این امر موجب میشود تا در طراحی رآکتور محدودیتهایی ایجاد شود. واکنشهای گازی نمونهای از واکنشهای همگن هستند که معمولاً در رآکتورهای لولهای انجام میشوند. رآکتورهای ناهمگن بر اساس فازهای درگیر در واکنش شکلهای مختلفی دارند اما نکته مهم در این رآکتورها ایجاد انتقال جرم و تماس مناسب بین فازها برای انجام واکنش است. در جدول زیر انواع راکتورهای شیمیایی ازنظر فازهای درگیر در واکنش و نمونههای صنعتی آن نشان دادهشدهاند
جدول ۲‑۱: انواع راکتورهای شیمیایی ازنظر فازهای درگیر در واکنش
نوع فرایند | نمونه صنعتی |
فرایند گاز–جامد | واکنش گاز کلر با اکسید اورانیوم برای تولید اورانیوم کلرید فرار • زدایش ناخالصی اکسید آهن از اکسید تیتانیوم با استفاده از گاز کلر • سوختن زغالسنگ • تولید گاز از زغالسنگ • تولید گاز هیدروژن از واکنش بخار آب و آهن • تولید کاربید سینامید از واکنش نیتروژن هوا با کلسیم کاربید • واکنش سوختن سنگ معدن سولفید آهن در هوا |
فرایند مایع-جامد | فرایند انتقال یون • تولید استیلن از واکنش آب و کلسیم کاربید • لیچینگ سنگ معدن اورانیوم با اسیدسولفوریک • واکنش اسیدسولفوریک و سدیم کلرید جامد با سدیم فسفات یاسدیم نیترات |
فرایند گاز-مایع | تولید سدیم تیوسولفات از واکنش گوگرد دی اکسید و محلول آبی سدیم کربنات و سدیم سولفید • تولید سدیم نیتریت از واکنش نیتریک اکسید و اکسیژن با محلول سدیم کربنات • تولیدسدیم هیپوکلریت از واکنش کلر با سدیم هیدروکسید • تولید آلومینیوم نیترات از واکنش آمونیاک و اسید نیتریک محلول • تولید اسید نیتریک از جذب نیتریک اکسید در آب • استخراج ید از واکنش گوگرد دی اکسید با محلول سدیم یدات • واکنش هیدروژنه کردن روغنهای گیاهی با گاز هیدروژن |
فرایند مایع-مایع | تولید سود سوزآور از واکنش آمالگام سدیم و آب • نیتروژن دار کردن ترکیبات آلی با محلول آبی نیتریک اسید • تولید صابون از واکنش محلولهای قلیایی و چربیها یا اسیدهای چرب • زدایش گوگرد از مشتقات نفتی با اتانول آمینها • واکنش محصولات پتروشیمی با اسیدسولفوریک |
فرایند جامد-جامد | تولید سیمان • تولید کاربید بور از واکنش اکسید بور و کربن • تولید سیلیکات کلسیم از آهک و سیلیکا • تولید کلسیم کاربید از واکنش آهک و کربن • فرایند لبلانک |
فرایند جامد-مایع-گاز | مایعسازی یا هیدروژنه کردن زغالسنگ در دوغاب نفتی |
رآکتور بسته و نیمه بسته
رآکتور بسته گونه سادهای از رآکتورهای شیمیایی هستند که بهصورت مخزنی همراه باهمزن و سیستم تبادل حرارت است. در این رآکتورها مواد اولیه داخل رآکتور پر میشود و سپس واکنش انجام میگیرد. پس از تکمیل واکنش و تولید محصول، درب رآکتور بازشده و محصولات تخلیه میشوند. این فرایند بارها و بارها قابل تکرار است. رآکتورهای نیمه بسته نیز به همین صورت است با این تفاوت که در این نوع از رآکتورها، مواد اولیه بهآرامی به مخزن افزوده میشود اما خروجی از رآکتور وجود ندارد. از رآکتورهای بسته عمدتاً در تولید محصول در ابعاد کم و محصولاتی که متقاضی مقطعی یا فصلی دارند استفاده میشود. موادی مانند مواد دارویی ازجمله موادی هستند که در دستگاههای بسته تولید میشود. تغییر در شکل فرایند با استفاده از رآکتورهای بسته بهمراتب آسانتر و بهصرفهتر از فرآیندهای پیوسته است. دانستن سینتیک و سازوکار فرایند در رآکتورهای بسته کماهمیتتر است به همین سبب است که سینتیک عمده فرآیندهای داروسازی ناشناخته است معادله عمومی رآکتورهای بسته به شکل زیر تعریف میشود.
با انتگرالگیری از معادله دیفرانسیل بالا در شرایط مرزی زیر به معادله عمومی رآکتور بسته برحسب غلظت خواهیم رسید.
رآکتورهای پیوسته
رآکتورهای پیوسته
شکل ۲‑۷: : نماد رآکتور سی اس تی آر
رآکتورهای پیوسته گونهای متداول از رآکتورها هستند که در آنها یک یا چند جریان ورودی به سیستم، مواد واکنشدهنده را به داخل رآکتور میآورد و پس از واکنش، از خروجی یا خروجیهای رآکتور محصولات خارج میشوند. بهطورمعمول دبی ورودی و خروجی از این رآکتورها ثابت است. در غیر این صورت امکان سرریز یا تخلیه سریع مخزن رآکتور وجود دارد. در زیر معادله کلی موازنه رآکتور پیوسته نوشتهشده است.
این نوع رآکتورها عمدتاً برای تولید محصولات با حجم بالا و محصولاتی که میزان تقاضای آنها بهصورت ثابت در بازار وجود دارد استفاده میشود. مواد سوختی، محصولات پتروشیمی و مواد شوینده و بهداشتی ازجمله این مواد هستند. ایجاد تغییرات در رآکتورهای پیوسته به دلیل اینکه در فرآیندهای پیوسته باید همه فرایندها با یکدیگر هماهنگ کار کنند بهمراتب سختتر از رآکتورهای بسته است. به همین دلیل از این نوع از رآکتورها در تولید یک محصول یا محصولاتی که تولید آن شباهت زیادی به هم دارند استفاده میشود. دو نوع متداول از رآکتورهای پیوسته، رآکتورهای مخزنی باهمزن و رآکتورهای پلاگ (یا لولهای) هستند:
رآکتور پلاگ
شکل ۲‑۸: طرح شماتیک از مقطع فرضی یک رآکتور پلاگ
رآکتورهای پلاگ گونهای از رآکتورهای پیوسته هستند که در آنها بهجای یک مخزن یا تانک، از یک لوله برای انجام واکنش استفاده میشود. این نوع رآکتورها نسبت به شکل مخزنی آن، فضای کمتری اشغال میکنند. درعینحال به دلیل ساختار لولهای، سطح تماس بیشتری با محیط اطراف داشته و تبادل گرما راحتتر انجام میشود. جریان پلاگ گونهای از جریان سیال در داخل لوله است که در آن سرعت حرکت سیال در نزدیکی دیواره لوله و در مرکز لوله یکنواخت است. این امر موجب میشود مواد واکنشدهنده بهطور یکنواخت با یکدیگر تماس یافته و واکنش انجام شود. این نوع از جریان با لولههای بلند و باریک ایجاد میشود. همچنین مارپیچ کردن لوله نیز میتواند به این امر کمک کند. معادله عمومی رآکتورهای پلاگ بهصورت زیر تعریف میشود:
همچنین رابطه زمان اقامت در این نوع رآکتور پیوسته بهصورت زیر است:
رآکتورهای مخزنی باهمزن
شکل ۲‑۹: داخل یک نوع رآکتور سی اس تی آر که در آن همزن و شفت آن به همراه بافلها (پایین تصویر) دیده میشوند
رآکتورهای مخزنی باهمزن که بهاختصار رآکتورهای سی اس تی آر نیز شناخته میشوند. این رآکتورها بهصورت مخازنی همراه با ورودیها و خروجیها هستند که عمل اختلاط و هم زدن مواد توسط شفت و پروانه صورت میگیرد. این نوع رآکتورهای پیوسته در مقایسه با رآکتورهای پلاگ حجم بیشتری نیاز دارند اما حجم تولید در آنها بالاتر است. معادله عمومی رآکتور برای این نوع از رآکتور برحسب غلظت بهصورت زیر تعریف میشود:
زمان اقامت در این نوع رآکتور نیز مشابه راکتور پلاگ بهصورت زیر قابلتعریف است:
رآکتورهای ثابت بستر و سیال بستر
گونه دیگری از رآکتورها، رآکتورهای ثابت بستر و سیال بستر هستند. در رآکتورهای ثابت بستر ماده جامد که معمولاً کاتالیست میباشد، بهطور ثابت داخل رآکتور قرار دارد و مواد واکنشدهنده پس از عبور از روی این مواد، واکنش داده و از رآکتور خارج میشوند. رآکتورهای آکنده نمونهای از این نوع رآکتورها هستند. نمونهای از کاربرد این نوع رآکتورها برای تصفیه گازهای خروجی از نیروگاههای سوخت فسیلی است. در این نوع نیروگاهها، پس از فرایند احتراق، گازهای حاوی ترکیبات مضر نیتروژن از داخل رآکتور حاوی کاتالیست عبور میکند تا ترکیبات مضر آن به مواد کمخطرتر تبدیل شوند. در رآکتورهای سیال بستر مواد جامد با جریانی از سیال در داخل رآکتور بهصورت معلق درمیآیند. این مواد جامد میتوانند واکنشدهندهها، کاتالیست ها یا بازدارندهها باشند. این فرایند موجب افزایش انتقال جرم و حرارت در رآکتور و اختلاط کاملتر اجزا میشود. از دیگر مزایای این نوع رآکتور امکان خارج کردن جامد از رآکتور بهصورت پیوسته و انتقال به واحد دیگر است. بهعنوان نمونه هنگامیکه احیا دوباره بازدارندهها و کاتالیست ها نیاز باشد، میتوان آنها را بهاینترتیب از رآکتور خارج و به واحد بازیابی منتقل کرد.
سنتز و پایداری نانوذرات مغناطیسی
تمرکز این مقاله بر روشهای مختلف سنتز، محافظت از نانوذرات سنتز شده و درنهایت عاملدار کردن این نانوذرات برای کاربردهای گوناگون است. تاکنون پیشرفت گستردهای در کنترل اندازه و شکل نانوذرات مغناطیسی با روشهایی مانند هم رسوبی، تجزیه حرارتی و روش هیدروترمال انجام پذیرفته است. بااینحال چالش اصلی، محافظت و جلوگیری از تخریب نانوذرات است که برای غلبه بر آن روشهایی مانند پوشش دهی با پلیمر، سیلیکا و کربن و یا قرار دادن آنها در یک ماتریکس بهکاربرده میشوند. درنهایت جهت بهکارگیری این نانوذرات درزمینهٔ های مختلف، سطح آنها را بهوسیله عاملدار کردن اصلاح نموده و بهبود میبخشند.
مقدمه
در سالهای اخیر، تلاشهای زیادی برای تهیه و سنتز نانوذرات مغناطیسی جهت کاربرد آنها درزمینهٔ های متنوعی مانند بیوتکنولوژی، دارورسانی، کامپیوتر و … انجامشده است. بهطورکلی عملکرد و کاربرد این نانوذرات تحت تأثیر طراحی و سنتز مناسب آنها است. تاکنون نانوذرات مغناطیسی مختلفی سنتز شدهاند که از آن جمله میتوان به نانوذرات فلزی خالص (Fe, Co , Ni)، اکسیدهای فلزی (Fe۳O۴ , γ-Fе۲О۳)، فریتها (MFe۲O۴ ,M = Cu, Ni, Mn, Mg, etc.) و آلیاژهای فلزی (FePt, CoPt) اشاره کرد.
در هنگام سنتز این نانوذرات بایستی برخی شرایط کلیدی مانند خواص مغناطیسی ذاتی ، اندازه و شکل نانوذرات، پوشش سطحی و بار سطحی نانوذرات، پایداری در محیط آبی و همچنین غیرسمیبودن آنها موردتوجه قرار گیرند. با انتخاب یک روش سنتز مناسب میتوان اندازه، شکل، پوشش سطحی و پایداری کلوئیدی نانوذرات مغناطیسی را بهصورت مطلوب کنترل کرد. در انتخاب ماده مغناطیسی، اکسیدهای آهن معمولاً حرف اول را میزنند. از یکسو این اکسیدها نسبت به دیگر نانوذرات مغناطیسی خواص مغناطیسی خوبی دارند و از سوی دیگر پایداری بالایی در برابر تخریب از خود نشان میدهند. همچنین این نانوذرات سمیت پایینتری را نیز دارند. تا به امروز روشهای گوناگونی جهت سنتز نانوذرات مغناطیسی ارائه و بهبود دادهشدهاند. در این مقاله به توضیح برخی از آنها پرداخته خواهد شد.
سنتز نانوذرات مغناطیسی
سنتز در فاز مایع
از روشهای سنتز نانوذرات مغناطیسی در فاز مایع میتوان به هم رسوبی (Coprecipitation)، میکرو امولسیون (Microemulsion)، سنتز با استفاده از فراصوت و … اشاره نمود. تهیه و رسوبدهی همگن ذرات با یکنواختی بالا (Monodispersity) را میتوان با اصول و نمودار LaMer (شکل ۲‑۱۰) توجیه نمود. رشد ذرات از دو راه نفوذ ذرات بر سطح هستههای از پیش تشکیلشده و تجمع برگشتناپذیر هستهها انجام میشود.
هم رسوبی (Co-precipitation)
روش هم رسوبی سادهترین و کارآمدترین روش شیمیایی برای سنتز نانوذرات مغناطیسی (اکسیدهای فلزی و فریتها) است. مزیت اصلی هم رسوبی، توانایی آن در سنتز تعداد زیادی از نانوذرات است. هرچند، کنترل توزیع اندازه ذرات در این روش محدود است و فاکتورهای سینتیکی رشد ذرات را کنترل میکنند.
فرآیند هم رسوبی (شکل ۲‑۱۱) شامل دو مرحله است: زمانی که غلظت گونهها به یک حد فوق اشباع میرسد مقدار کمی هستهزایی رخ میدهد و سپس رشد تدریجی هستهها (با نفوذ حل شوندهها بر روی سطح ذرات) صورت میپذیرد.
شکل ۲‑۱۱: شماتیک سنتز نانوذرات مغناطیسی Fe۳O۴ با استفاده از روش هم رسوبی؛ ابتدا محلولی از یونهای آهن در اسیدکلریدریک تهیهشده و سپس این محلول بر روی محلولی از دی ایزوپروپیل آمین (DIPA) ریخته میشود که نتیجه آن ایجاد رسوبی از نانوذرات اکسید آهن خواهد بود.
اخیراً استفاده از برخی ترکیبات آلی مانند پلی-وینیل الکل (PVA) که هم نقش کاهنده و هم نقش پایدارکننده را ایفا میکنند، باعث سنتز نانوذرات با یکنواختی بیشتری شده است.
معمولاً سنتز نانوذرات اکسید آهن (Fe۳O۴ , γ-Fе۲О۳) و فریتها در محیط آبی و به روش هم رسوبی از طریق واکنش زیر صورت میگیرد:
که در آن M+۲ میتواند عناصر متفاوتی ازجمله Fe۲+, Mn۲+, Co۲+, Cu۲+, Mg۲+, Zn۲+ ,Ni+۲ باشند[۱۲].
میکرو امولسیون (Microemulsion)
میکرو امولسیون مجموعهای غیرقابل اختلاط از حلال آبی، حلال آلی است که بهوسیله سورفاکتانت (Surfactant) پایدار میشوند. در این حالت قطراتی از حلال آبی که توسط لایهای از سورفاکتانت پوشیده شدهاند در بین حلال آلی به وجود میآید و به مجموعه آنها مایسل (Micelle) گفته میشود. همانطور که در شکل ۲‑۱۲، مشاهده میگردد، اگر قسمت آبگریز مولکول (بهاصطلاح قسمت هیدروکربنی) سورفاکتانت به سمت بیرون و حلال آلی باشد به آنها مایسل معکوس (Reverse Micelle) میگویند. اندازه مایسل بهدستآمده با نسبت مولی آب به سورفاکتانت تعیین میشود. از میکرو امولسیون آب در روغن (Water-in-Oil، W/O) بهطور وسیعی برای سنتز یکنواخت نانوذرات استفاده میشود. با مخلوط کردن آب، روغن و مواد واکنشدهنده، بهصورت مداوم قطراتی تشکیلشده، باهم برخورد کرده، ادغام میشوند و مجدداً شکسته میشوند که درنهایت منجر به تشکیل رسوب خواهد شد. با افزودن حلالهایی مانند استون و یا اتانول، میتوان رسوبها را لخته نمود و سپس با فیلتر کردن و یا سانتریفیوژ، آنها را از میکرو امولسیون جدا نمود. ازجمله معایبی که کارآمدی این فرآیند را کم میکند، استفاده زیاد از حلال میباشد[۱۳].
شکل ۲‑۱۲: شماتیکی از مایسل نرمال و معکوس
تجزیه حرارتی (Thermal Decomposition)
با تجزیه حرارتی برخی مواد اولیه آلی-فلزی در دمای بالا، مانند کمپلکسهای فلزی با لیگاندهای آلی، کربونیل فلزات (مانند Fe(CO)۵) یا برخی ترکیبات دیگر همراه با استفاده از حلالهای آلی و سورفاکتانتهای مانند اسیدهای چرب، اولئیک اسید و هگزا دسیل آمین (Hexadecylamine)، میتوان نانوذراتی با یکنواختی و اندازه بسیار کنترلشده را سنتز نمود.
در این نوع سنتزها، نسبت مواد اولیه یعنی ترکیبات آلی– فلزی، سورفاکتانت و حلال پارامترهای اصلی برای کنترل اندازه و ریختشناسی سطح (Morphology) نانوذرات مغناطیسی به شمار میآیند. دما و زمان واکنش و همچنین دوره هضم رسوب (Aging) نیز ممکن است برای کنترل دقیق اندازه و مورفولوژی بسیار مهم باشند[۱۳] .
تجزیه حرارتی مواد اولیه با فلز مرکزی کاتیونی، مستقیماً منجر به تولید نانوذرات اکسید فلزی میشود. از سوی دیگر، اگر از پیشمادههای صفر ظرفیتی مانند کربونیل ها استفاده شود، تجزیه حرارتی در ابتدا سبب تولید نانوذرات فلزی میشود و میتوان پسازاین مرحله با استفاده از هوا و یا اکسیدکنندهها نانوذرات اکسید فلزی را تولید کرد .
روشهای دیگر
علاوه بر روشهای گفتهشده روشهای متعدد دیگری مانند هیدروترمال و استفاده از امواج فراصوت نیز استفاده میشود. هیدروترمال (Hydrothermal)، روشی سنتزی است که در محیط آبی و دمای بالا انجام میشود. این دمای بالا سبب تسریع در هستهزایی و رشد نانوذرات و درنهایت به وجود آمدن نانوذرات بسیار ریز (Ultrafine) میشود[۱۴].
روش دیگر، سنتز با استفاده از امواج فراصوت (سنتز نانومواد با استفاده از روشهای سونوشیمیایی) است. مبنای استفاده از این روش، بر پایه فرایندی به نام حفرهزایی (Cavitation) استوار است که براثر تشکیل، رشد و انفجار حبابها در داخل مایع صورت میپذیرد. در اثر انفجار درونی این حبابها، گرمای موضعی زیادی به وجود میآید که میتوان ازآنجهت انجام واکنشهای مختلف بهره برد.
سنتز در فاز گاز
در فاز گازی نیز مانند فاز مایع، روشهای مختلف برای سنتز نانوذرات استفاده میشود. روشهای مورداستفاده در این فاز رسوبدهی شیمیایی بخار (Chemical Vapour Deposition)، تخلیه با قوس الکتریکی (Arc Discharge) و پیرولیز با لیزر (Laser Pyrolysis) هستند.
رسوبدهی شیمیایی بخار (Chemical Vapour Deposition)
در فرایند رسوبدهی شیمیایی بخار (CVD) مقادیر کمی از پیشمادهها توسط جریان گاز وارد یک محفظه داغ میشوند و رسوبدهی تحت خلأ در دمای بالا (>900 °C) انجام میگیرد. رشد و تجمع (Agglomeration) ذرات توسط جریان سریع گاز در خروجی محفظه کاسته میشود. فرایندهای حرارتی (Thermal Treatment) پس از سنتز نانو پودرهای بهدستآمده اجازه میدهد تا تغییرات ساختاری شامل خلوص ذرات و تبلور، و همچنین تغییر بهاندازه و ساختار و مورفولوژی دلخواه بهخوبی انجام پذیرد[۱۴].
تخلیه با قوس الکتریکی (Arc Discharge)
این روش عموماً برای سنتز نانوذرات مغناطیسی محصورشده با یک لایه کربنی (Carbon-Encapsulated) یا نانوذرات مغناطیسی از جنس کاربید فلزات مورداستفاده قرار میگیرد. طی این روش، پیشماده فلزی درون حفرهای بر روی یک الکترود گرافیتی قرار گرفته و در اثر تخلیه الکتریکی بهصورت قوس، تبخیر میشود. از این روش همچنین میتوان برای پوشاندن سطح نانوذرات فلزی با نیترید بور (Boron Nitride) استفاده نمود. متأسفانه به دلیل محدودیتهایی همچون بازده پایین و دشواری در کنترل اندازه و ضخامت نانوذرات سنتز شده، نمیتوان این روش را در مقیاس صنعتی به کار برد .
در کنار این روشها از نور لیزر نیز میتوان برای سنتز نانوذراتی با توزیع اندازه کمتر از ۱۰ نانومتر استفاده نمود [۱۴].
سنتز در فاز جامد
برای سنتز نانوذرات مغناطیسی در فاز جامد (بهخصوص نانوذرات محصورشده با یک لایه کربنی) عموماً از روشی تحت عنوان Annealing استفاده میشود که در اصل به معنای حرارت دادن در دمای بسیار بالا و سپس سرد کردن است. مزیت استفاده از این روش، کنترل خوب اندازه و خاصیت سوپر پارامغناطیسی نانوذرات و همچنین کاهش ناخالصیها و سنتز مناسب در مقیاس بالا است.
روشهای محافظت (Protection Methods)
هر چند تا به حال، روشهای متعددی در جهت پیشرفت و بهبود روشهای سنتز نانوذرات مغناطیسی ارائه شده است، پایدار ماندن این نانوذرات برای مدت طولانی در برابر انباشته شدن و رسوب دادن آنها موضوعی مهم و قابل توجه است. چرا که پایداری این نانوذرات امری مهم در به کارگیری آنها است.
نانوذرات مغناطیسی به دلیل سطح ویژه بزرگی که دارند در برابر اکسیداسیون و انباشتگی بسیار حساس و همچنین از لحاظ شیمیایی بسیار واکنش پذیر هستند. در دما و فشار معمولی، سطح نانوذرات بهسرعت اکسید شده و درنتیجه لایهای نازک از اکسید بر روی آن تشکیل میشود که به شدت خواص آنها را تغییر میدهد. انباشتگی طبیعی نانوذرات مشکل دیگری است که کاربرد گسترده نانوذرات مغناطیسی را با محدودیت مواجه میکند[۱۴].
- از روشهای زیر میتوان جهت پایداری نانوذرات مغناطیسی استفاده کرد:
تعادل بین نیروهای دافعه و جاذبه بین نانوذرات.
قرار دادن پوشانندههای آلی هایا معدنی بر روی سطح نانوذرات مغناطیسی.
پوششهای آلی(Organic Coating) : تا به امروز اغلب مطالعات بر روی توسعه پوشش با سورفاکتانتها متمرکز شده بود، اما امروزه بیشتر توجهات بدلیل ایجاد دافعه بیشتر به سمت پوشش دهی با پلیمرها معطوف شده است. روشهای متعددی برای پایداری نانوذرات مغناطیسی با استفاده از سورفاکتانتها و پلیمرها چه در حین سنتز و چه بعد از سنتز نانوذرات ارائه شده است. همانطور که در شکل ۲‑۱۳، نشان داده شده است، با ایجاد یک یا دو لایه بر روی آن سبب ایجاد دافعه و پراکنده (Disperse) ماندن نانوذرات مغناطیسی میشوند.
شکل ۲‑۱۳: برخی از پوشش های آلی مورداستفاده جهت تضمین پایداری نانوذرات مغناطیسی
جهت جلوگیری از اکسید شدن نانوذرات مغناطیسی، بایستی پوشش دهی بهصورت متراکم باشد، زیرا یک یا دولایه نازک در محیط اسیدی بهراحتی از سطح نانوذرات جدا میشوند و سبب از دست رفتن خاصیت مغناطیسی میگردد.
پوششهای معدنی (Inorganic Coatings)
سطح نانوذرات مغناطیسی را میتوان با پوششهای معدنی (شکل ۵) همچون اکسیدهای فلزی، سیلیکا، فلزات گرانبها و کربن پوشاند.یک راه بسیار ساده برای محافظت نانوذرات مغناطیسی، استفاده از اکسیدهای فلزی متفاوت از هسته اصلی بهعنوان پوشش آنها است.
شکل ۲‑۱۴: تصویر TEM از نانوذرات مغناطیسی پوشیده شده با سیلیکا
همچنین فلزات گرانبها مانند طلا، به دلیل واکنشپذیری کم و توانایی ایجاد پل با دیگر گروههای عاملی، را نیز میتوان برای محافظت از هستههای مغناطیسی مورداستفاده قرار داد. در این حوزه استفاده از پوششهایی با جنس سیلیکا و کربن نیز به دلیل مسائلی همچون ارزان قیمت بودن، سمیت کم، خصلت زیست سازگاری مناسب و… توجه بسیاری را به خود منعطف نمودهاند.
عاملدار کردن نانوذرات مغناطیسی (Functionalization of Magnetic Nanoparticles)
برهمکنشهای بین نانوذرات و محیط اطراف آنها به شدت تحت تأثیر سطح و گروههای سطحی نانوذرات است. توسعه روشهای اصلاح سطح نانوذرات مغناطیسی جهت عاملدار کردن شیمیایی آنها و کنترل حلالیتشان مهم است و به شدت متاثر از نوع کاربرد مورد نظر است. بهطور مثال برای کابردهای بیولوژیکی اغلب سطح نانوذرات مغناطیسی با مولکولهای زیستی مانند پروتئینها اصطلاح میشوند.اکثر کاربردهای نانوذرات مغناطیسی نیازمند پایداری شیمیایی، یکنواختی در اندازه و پراکندگی مناسب آنها در محیط مایع است. لذاسطح نانوذرات باید با گروههای مناسب اصلاح شوند. جذب شیمیایی الکترواستاتیکی (یا افزودن لیگاند، در علم شیمی لیگاند به یون یا مولکولی گفته میشود که قادر است به یک فلز یا چند فلز خاص متصل شده و تشکیل یک کمپلکس دهد) و اتصال کووالانسی (تعویض لیگاند[۱]– ازجمله روشهایی هستند که برای تغییر و اصلاح سطح نانوذرات استفاده میشوند[۱۵].
نتیجه گیری
پیشرفتهای صورت گرفته در سنتز نانوذرات مغناطیسی به ویژه در دو دهه اخیر، موجب توسعه طیف گستردهای از این نانوذرات، آن هم در اندازههای مختلف و قابل کنترل شدهاست. بااینحال، یکی از مشکلات غیر قابل اجتناب در ارتباط با این نانوذرات، عدم پایداری ذاتی آنها در بازههای طولانی مدت است. از سوی دیگر، مسائلی همچون واکنش پذیری بسیار بالا و سمیت برای برخی از نانوذرات مغناطیسی، کاربرد آنها را با محدودیت مواجه مینماید. پژوهشهای صورت گرفته در این حوزه بهخوبی نشان دادهاند که برای غلبه بر این مشکلات، پوشش دهی این نانوذرات با استفاده از مولکولهای آلی و معدنی یکی از موثرترین راهکارها به شمار میآید. به نحوی که در سالهای اخیر، عاملدار کردن و اصلاح سطح نانوذرات مغناطیسی، پتانسیل استفاده از این نانوذرات درزمینهٔ های متفاوت را بهصورت چشمگیری افزایش داده است.
فرایند هیدروترمال برای تولید مواد؛ گذشته، حال و آینده
روش هیدروترمال امکان تولید مواد پیشرفته مانند تکبلورهای توده، ذرات ریز (fine particle) و یا نانوذرات را فراهم میکند. دراین مقاله مزایای فناوری هیدروترمال در مقایسه با روشهای موسوم تولید مواد، مورد بحث و بررسی قرارگرفته، روندهای رایج تولید مواد، در ارتباط با مفهوم فراورش محلولهای نرم (processing soft solution) بهعنوآنیک روش ساخت تک مرحلهای با مصرف حداقل انرژی توصیف شده، و درنهایت مروری بر چشم انداز گذشته، حال، آینده فناوری هیدرترمال بهعنوان ابزاری برای ساخت مواد پیشرفته ارائه شده است.
مقدمه
واژه هیدروترمال، از منشا زمینشناختی است. از این واژه برای اولین بار یک زمین شناس انگلیسی به نام رودریک مورخیسان (Sir Roderick Murchison) در توصیف عمل آب در دما و فشارهای بالا، که باعث ایجاد صخرهها و کانیهای گوناگون میشود، استفاده کرد. بزرگترین تکبلورهای موجود در طبیعت (بلور یاقوت) و بیشترین مقدار تک بلوری که بشر در آزمایشگاه تولید کرده است (بلور کوارتز به مقدار ۱۰۰۰ کیلوگرم)، هر دو منشا هیدروترمال دارد.
یوشیمورا و بیراپا (Byrappa,Yoshimura) در سال ۲۰۰۱ از فرایند هیدروترمال بهعنوان واکنش شیمیایی همگون یا غیر همگون در حضور حلال (خواه آبی باشد یا غیر آبی) در دمای بالاتر از اتاق و در فشار بزرگتر از یک اتمسفر در یک سیستم بسته یاد کردند.
به هر حال هنوز درباره استفاده از واژه هیدروترمال نظر واحدی وجود ندارد؛ مثلا شیمیدانان ترجیح میدهند که برای توصیف واکنشهای شیمیایی در حضور حلالهای غیر آبی یا حلال در شرایط بحرانی یا نزدیک بحرانی، از واژه سولوترمال (solvothermal) استفاده کنند، همین طور اصطلاحات دیگری مانند حرارت در محیط آمونیاکی یا الکلی (alcothermal , ammonothermal) و … وجود دارد. علاوه بر این، موضوع دیگری هم هست که در مورد شرایط فوق بحرانی برای تولید مواد بحث میکند. از حلالهای فوق بحرانی (آب و دی اکسید کربن) عموما برای انجام گستره وسیعی از واکنشهای شیمیایی بهعنوان جایگزین حلالهای آبی (شامل ساخت نانوذرات، فرایند استخراج مواد شیمیایی، بازیابی فاضلاب (waste treatment) و …) استفاده میشود. بیشتر محققان، این فرایند را «فرایند سبز یا شیمی سبز» مینامند. مواد پیشرفته، مواد شیمیایی (خواه آلی یا معدنی یا هیبرید) دارای خواص شیمیایی یا فیزیکی دلخواهی هستند. تمرکز اصلی این مقاله بر مرور تولید این مواد پیشرفته است. چندین روش برای تولید مواد پیشرفته استفاده میشود که عبارتند از: نشست بخار شیمیایی، رویکرد شیمی کلوئیدی (colloidal chemistry Approach)، آسیاب کاری مکانیکی، آلیاژ کردن مکانیکی، سل-ژل، هیدروترمال، تقلید از طبیعت (biomimitic)، پیرولیز شعله، سایش لیزری (laser ablation)، روش اولتراسونیک، فرایند الکترونشست، سنتز در محیط پلاسما، روش میکروموج و …. از میان این روشها، تنها روش هیدروترمال سهمی تقریبا معادل ۶ درصد را به خود اختصاص داده است. این روش ساخت سادهترین و سختترین مواد با خواص فیزیکی- شیمیایی دلخواه را فراهم میسازد. این روش در مقایسه با سایر روشهای مرسوم مزایایی دارد که میتوان به ذخیره انرژی، سادگی، قیمت ارزان، کنترل هستهزایی بهتر، عاری از آلودگی (چون واکنش در محیط بسته انجام میشود)، پخششدگی بهتر، سرعت بالای واکنش، کنترل شکل بهتر، دمای عملیاتی کمتر در حضور حلال مناسب و … اشاره کرد، همچنین استفاده از آن باعث سرعت گرفتن بر هم کنش بین پودر جامد و حلال مایع و تولید مواد هم گون و فاز خالص میشود؛ سینتیک واکنش زیاد میشود؛ سیال هیدروترمال قدرت پخش و نفوذ بیشتری را ارائه میکند؛ ویسکوزیته کمتر، انتقال جرم را تسهیل کرده و در عوض توان حل کنندگی را بیشتر میکند و مهم تر از همه اینکه، محیط شیمیایی واکنش بهطور مناسب دنبال میشود. اگرچه این فرایند در مقایسه با فرایند آسیاب کاری یا نشست بخار به زمان بیشتری نیاز دارد؛ تولید ذرات بلورین را با کنترل بهتر اندازه و شکل فراهم میسازد. در سالهای اخیر از طریق محاسبات ترمودینامیکی، توجه بیشتری به شیمی محلول فرایند هیدرترمال شده است که منجر به انتخاب آسان حلال مناسب و گستره دمایی-فشاری مناسب میشود. گستره وسیعی از عناصر بومی، اکسیدهای فلزی، هیدروکسیدها، سیلیکاتها، کربناتها، فسفاتها، سولفیدها، تلوریدها، نیتریدها، ذره یا نانوساختارهایی مانند نانولوله، نانوسیم، نانومیله و … با استفاده از این روش به دست میآید. از این روش در سنتز شکلهای مختلف کربن مانند (sp۳،sp²) و انواع حد واسط نیز میتوان استفاده کرد.
روندهای رایج در فناوری هیدروترمال
اختلافات زیادی بین تحقیقات هیدروترمال-که این در گذشته و قرن اخیر (۲۱) انجام میشده است- وجود دارد. در اواسط قرن۲۰، فناوری هیدروترمال بیشتر بر روی دما و فشار بالا تمرکز داشت، زیرا از حلالیت مواد اطلاعاتی نداشتند و حلال مناسبی را نیز انتخاب نکرده بودند. اولین همایش بین المللی هیدروترمال در سال ۱۹۸۲، در سازمان فناوری توکیو با حضور دانشمندان و متخصصان علوم بینرشتهای برگزار شد. از آن پس اطلاعات در مورد شیمی فیزیک، روابط PVT در سیستم هیدروترمال بهبود یافت، که به کاهش چشمگیر شرایط دما و فشار این فرایند کمک کرد، همچنین فرایند سولوترمال و فوق بحرانی (که از حلالهای دیگر مثل مواد آلی، کمپلکسهای آلی فلزی استفاده میکرد) منجر به سوق دادن این فناوری به سمت شیمی سبز شد. جدول (۱) تمایلات موجود در فرایند هیدروترمال برای تولید مواد و سوق دادن به سمت شیمی سبز برای پیشرفتهای بشر را نشان میدهد، زیرا این روش انرژی کمی مصرف میکند، ضایعات جامد یا مایع یا گاز ندارد، نیازی به عملیات بازیابی و گزینش گزینش پذیری بالا ندارد و سیستم بیخطر و بستهای است. امروزه اکثر تحقیقات هیدروترمال بر اساس مدلسازی هوشمند واکنشهای هیدروترمال صورت میگیرد، این امر به پیش بینی شرایط واکنش کمک کرده، فازی دلخواه با کنترل شکل و اندازه به دست میدهد. مدلسازی براساس اصول ترمودینامیک است و امروزه نرم افزارهایی تجاری برای محاسبات ترمودینامیک وجود دارد.
جدول ۲‑۲: پیشرفت هیدروترمال تولید مواد پیشرفته
مفاهیم جدید در فناوری هیدروترمال
در سالهای اخیر، اضافهشدن انرژیهای خارجی مانند انرژی میکروموج، ماورای صوت، مکانیکی – شیمیایی، الکتریکی، مغناطیسی و …. به فرایند هیدروترمال، فصل جدیدی از تولید مواد را باز کرده است که بهعنوان فرایندهای چند انرژی ارجاع داده میشود؛ زیرا تاکنون در روش هیدروترمال، محققان با سه متغیر دما، فشار، پتانسیل شیمیایی تقریبا قادر به حل اغلب مسائل ترمودینامیکی موجود در فرایند هیدروترمال بودهاند، این در حالی است که اما با اضافه شدن متغیرهای انرژی اضافه به سیستم، روابط ترمودینامیکی کاملا متفاوت و پیچیده شده است. در طی یک سال گذشته، محققان برای دستیابی به نانوذرات دلخواه خود در کوتاهترین زمان ممکن و با خواص فیزیکی معین، از مفهوم واکنشهای هیدروترمال استفاده کردهاند که این تلاش همچنان ادامه دارد. پایه و اساس مفهوم فراورش محلول نرم یوشیمورا، براساس فرایندهایی ملهم از طبیعت و انرژی لازم برای انجام فرایند هستند. شکل (۱) انرژی را در مقایسه با کارایی تنوع فرایندهای زیستی و مصنوعی نشان میدهد. فراورش نرم بهعنوان سومین ناحیه، بین فرایندهای مصنوعی زیستی و مصنوعی قرار دارد. فرایندهای زیستی میتواند موادی مفید با مصرف انرژی کم تولید کند که اندازه شکل محدودی دارند؛ در حالی که فرایندهای دست ساز بشر تقریبا قادر به تولید تمام مواد بوده و انرژی زیادی هم مصرف میکند، همچنین فرایندهای نرم تولید مواد با کارایی بالا را که تحت شرایط ملایم قرار دارند، و مورد هدف قرار میدهد. فرایندهایی که در گروه فراورش محلول نرم قرار میگیرند، در شکل ۲‑۱۵، دیده میشود.
شکل ۲‑۱۵ : انرژی در مقایسه با کارایی / تنوع در فرایندهای زیستی و دست ساز بشر
شکل ۲‑۱۶: شماتیک مقایسه تولید تکمرحلهای و چند مرحلهای مواد پیشرفته
این شکل تولید مواد پیشرفته (شامل فرایندهای تک مرحلهای در مقایسه با فرایندهای چندمرحلهای) را نشان میدهد. بزرگترین مزیت فرایند هیدروترمال این است که کنترل سطح، مورفولوژی و اندازه را بهصورت درجا آسان میکند.
فرایند هیدروترمال یکی از مهمترین روشها در فراورش محلول نرم است. پارامتر کلیدی فراورش در حالت محلول، حلال است. در مورد فرایند هیدروترمال، حلال چندین نقش را بر عهده دارد و برای روشن شدن سازوکار واکنش انجامشده تحت شرایط هیدروترمال، درک نقش حلال ضروری است. شکل ۲‑۱۷، تأثیر حلال هیدروترمال بر مواد جامد را از تأثیر فیزیکی بهعنوان محیط P,T، تا تأثیر شیمیایی بهعنوان واکنشگر نشان میدهد.
شکل ۲‑۱۷: نقشهای مایع هیدروترمال بر روی نمونه جامد حلال میتواند بهعنوان جاذب، واکنشگر و یا حلال عمل کند
فراورش هیدروترمال ذرات ریز
از زمان تولد فناوری هیدروترمال، فراورش ذرات ریز تحت شرایط هیدروترمال معروف بوده است. اغلب آزمایشهای هیدروترمال معروف بوده است. اغلب آزمایشهای هیدروترمال در طول دهه ۱۸۴۰ تا ۱۹۰۰ در مورد محصولات ریز تا نانوبلورها بحث میکرد که به علت نبود ابزارهای پیچیده برای امتحان ریز بودن محصول به شکست انجامید.
در طول این مدت بسیاری از آزمایشها بر روی سنتز ذرات ریز، زئولیت، خاک رس، بعضی سیلیکاتها، هیدروکسیدها و … انجام میشد. با گزارشی که برر (Berrer) درباره سنتز هیدروترمال ذرات ریز زئولیت در طول دهه ۱۹۴۰ ارائه کرد، شاخه جدیدی از علم یعنی فناوری الک کردن مولکولها (Molecular sieve technology)، باز شد. تحقیقات هیدروترمال انجامشده در طول دهه ۱۹۹۰، شروع کار روی تولید ذرات ریز و خیلی ریز با کنترل اندازه و شکل را نوید میدهد. امروزه، این روش بهعنوآنیکی از روشهای بسیار موثر شیمی نرم (soft chemistry) در تولید مواد پیشرفته مانند ذرات نازک یا نانومواد با کنترل اندازه و شکل محسوب میشود. جدول زیر مقایسه روشهای مختلف تولید انواع پودر را نشان میدهد.
جدول ۲‑۳: مقایسه روشهای سنتز پودرهای گوناگون
بر اساس جدول بالا، روش هیدروترمال، برای تولید پودرهای خیلی ریز با خلوص بالا، استوکیومتری کنترل شده، کیفیت بالا، توزیع اندازه ذرات باریک، مورفولوژی کنترل شده، هم شکل بودن، نقایص کمتر، ذرات فشرده (Dense particle)، بلورینگی بالا، تکرارپذیری بالا، کنترل میکروساختار، واکنش پذیری و قابلیت تراکم بالا (High sinterability) و … روش ایده آلی است. شکل (۴) اختلافات مهم در محصولات بهدستآمده با آسیاب گلولهای، زینترکردن (sintering) و احتراق با روش هیدروترمال را نشان میدهد.
شکل ۲‑۱۸: مقایسه تولید مواد با روش هیدروترمال با سایر روشهای مرسوم
فناوری هیدروترمال برای فناوری نانو
چالش اساسی در علم نانومواد، کنترل دقیق اندازه و شکل است که مستقیما به روشهای تولید مواد مربوط میشود. نانوذرات از طریق روشهای گوناگونی مثل تبدیل جامد به جامد، مایع به جامد یا گاز به جامد به دست میآید. بیشترین نیازها برای کاربردهای زیست شناختی (مانند درمان، تصویرگیری زیستی، دستگاههای انتقال دارو، حسگرهای زیستی، (MRI (Magnetic Imager Resonance))، میکروالکترونیکها، به کنترل اندازه و شکل نانومواد اصرار دارد؛ از این رو، روشهایی در فاز محلول مانند هیدروترمال، یکی از با ارزشترین روشهای ساخت نانومواد در سالهای اخیر شمرده میشود و به دلیل کیفیت بالای محصولاتی که از این روش بهدستآمده، نسبت به سایر روشها ارجحیت دارند. دسته وسیعی از نانومواد با استفاده از روش هیدروترمال بهدستآمده است، از میان آنها عناصر بومی، اکسیدهای فلزی، هیدروکسیدها، سیلیکاتها، کربناتها، فسفاتها، سولفیدها، تلوریدها، نیتریدها، سلنیدها و … را با شکلهای نانولوله، نانوسیم، نانومیله و … میتوان نام برد. از این روش در سنتز شکلهای گوناگون کربن مانند SP²،SP3 و حالت حد میانی آنها نیز استفاده میشده است. یوشیمورا و گروهش کارهای با ارزشی روی ساخت و پایداری نانوشکلهای کربن و CNTs، تحت شرایط هیدروترمال فوق بحرانی انجام داده است. آنها پیشنهاد کردند که از هر نوع منبع کربن مایع، جامد یا گاز میتوان در سنتز هیدروترمال فوق بحرانی استفاده کرد. با کنترل شرایط آزمایش، آنها قادرند شکلهای مختلف کربن شامل CNTs با ساختارهای گوناگون را ایجاد کنند. شرایط آزمایشی که این گروه استفاده کرد، عبارتند از: T=550-800°Cبالاتر از P=100Mpa شکل زیر نشاندهنده بعضی از شکلهای کربنی است که یوشیمورا و همکارانش به دست آوردهاند.
شکل ۲‑۱۹: . نانوساختارهای کربن بهدستآمده از واپاشی کاربید فلزات تحت شرایط هیدروترمال فوق بحرانی
روندهای آینده تحقیقات هیدروترمال
فناوری هیدروترمال (خواه هیدروترمال یا سولوترمال یا فوق بحرانی) به دلیل داشتن مزایای چندوجهی در تولید، گستره وسیعی از مواد پیشرفته (از بلورهای تودهای تا نانوبلورها و نانوذرات) چشم انداز خوبی دارد. از این فناوری در چند سال گذشته در رشد بلورهای راهبردی مانند GaN، GaPO4،ZnO و … بهطور چشمگیری استفاده میشد. تولید ذرات ریز و نانوذرات بهعنوآنیک ابزار جذاب در حال رشد است. اخیرا مفهوم فناوری هیدروترمال چند انرژی شروع شده است که به دلیل سرعت، هزینه، راحتی و آرام بودن به لحاظ محیطی نقشی حیاتی ایفا میکند. برای تولید در مقیاس صنعتی، مواد هیدروترمال فوق بحرانی، بهخصوص سیالهای فوق بحرانی O۲ و H۲O نقش بزرگتری برای گروه گستردهای از مواد بهعنوان بخشی از شیمی سبز ایفا میکند و در آینده نیز فرایندهایی برای تولید مواد استفاده خواهد شد که دارای خصوصیاتی باشند، مثل عدم اتلاف انرژی، داشتن شرایط محیطی ملایم که منجر به گرمشدن جهان نشود. روش فراورش محلول نرم تمامی شرایط بالا را داراست و ابزار توانمندی برای تولید مواد به شمار میرود. در روش فراورش محلول نرم، محلول پیشماده مهم است. بسیاری از محققان پیشبینی کردهاند که ترکیب پلیمریزاسیون سل-ژل با هیدروترمال تحت شرایط ملایم، توانایی زیادی برای تولید مواد دارد؛ مثلا در روشی که یوشیمورا پیشنهاد کرده است، کمپلکس تیتانیوم محلول در آب برای سنتز بروکیت (Brokite) روتیل و آناتاز تحت شرایط هیدروترمال، پایهای برای فرایندهای تولید دوستدار محیط زیست خواهد بود. چنین رویکردی نتایج مفیدی برای تولید الکتروسرامیکهایی حتی در دمای بالا مانند SrTiO۳ ، BaTio۳ و … دارد. همچنین شیمی ژل آلکوکسیدهای فلزی مسیری را برای تهیه پیشماده مواد پیشرفته با روش هیدرو ترمال تهیه میکند. از این رو رویکردهای بین رشتهای محلولهای موثر برای راهبردهای آینده تولید مواد خواهد بود که ازنظر محیطی ملایم و ازنظر هزینه موثرند. فناوری هیدروترمال ابزار قدرتمندی در ترکیب با سل-ژل و فرایندهای چند انرژی، حتی برای دستگاههای چند جزئی خواهد بود.
نتیجه گیری
فناوری هیدروترمال ابزاری قدرتمند در تولید مواد محسوب میشود؛ زیرا ازنظر محیطی ملایم و بسیار مناسب برای تولید مواد پیشرفته (از تک بلور تودهای تا ذرات خیلی ریز و درنهایت نانوبلور یا نانوذرات) است. فرایندهای بدون ضایعات (Wasteless process)، آینده تولید مواد از لحاظ شرایط محیطی ملایم خواهند بود، بدون اینکه منجر به گرمی زمین شوند. پیشرفتها در شیمیفیزیکی و شیمی محلولهای محیط هیدروترمال که منجر به مدل سازی واکنشهای هیدروترمال شده است، به مهندسی هوشمند مواد تحت شرایط PT کاهش یافته کمک میکند. استفاده از دستگاههای چند انرژی مانند میکروموج – هیدروترمال، الکتروشیمی- هیدروترمال، مکانوشیمی – هیدروترمال، صوت- هیدروترمال و … این فناوری را به مسیرهای کاوش نشده در قرن ۲۱ پیش برده است. با اضافهشدن انرژی اضافی متغیرها و روابط ترمودینامیکی، سیستم متفاوت و اغلب پیچیدهتر میشود. با استفاده از عامل پوشاننده و عوامل فعال سطحی (surfactant) و سایر مولکولهای آلی یا زیستی، برای اصلاح سطح این نانو بلورها، خواص فیزیکی-شیمیایی مورد دلخواه به دست میآید. ترکیب فناوری هیدروترمال و فناوری نانو میتواند پاسخ مشکلات موجود در تولید مواد پیشرفته در قرن ۲۱ را بدهد، همچنین ترکیب پلیمریزاسیون سل-ژل و هیدروترمال، توانایی زیادی در تولید تحت شرایط ملایم مواد دارد. تمامی این مزایا برای فناوری هیدروترمال چشم انداز امیدوارکنندهای را در قرن ۲۱ برای تولید مواد پیشرفته ارائه میکند.
واکنشهای سولوترمال: مسیری اصلی برای سنتز مواد جدید
۲۰ سال پس از اولین پیشرفت واکنشهای سولوترمال، پیگیری تمایلات آینده و توانمندیهای این روش، مهم به نظر میرسد. در طول ۲۰ سال گذشته، از واکنشهای سولوترمال برای تهیه میکرو-نانوذرات با مورفولوژیهای مختلف استفاده میشده است. واکنشهای سولترمال با شاخصهای شیمیایی مختلف (ماهیت واکنشگر و حلال) و شاخصهای ترمودینامیکی (بهخصوص دما، فشار) شناخته میشوند. الف) انتخاب ترکیب حلال، حیطه تحقیقاتی جدیدی را برای پایدارکردن طبقات مختلفی از مواد از قبیل آلیاژها، اکسیدها، نیتریدها، سولفیدها و … بازکرده است؛ ب) شرایط دمایی ملایم که میتواند نفوذ شیمیایی و واکنش پذیری را بهبود بخشد تا اینکه به تهیه مواد ویژه در مرز بین طبقات مختلف موادی از قبیل مواد آلی (اکسیدها، نیتریدها، هالیدها و غیره) یا آلی-معدنی، معدنی-زیستی کمک کند؛ ج) شرایط فشار بالا، به دلیل انتقال کم انرژی در مقایسه با دما، اجازه میدهد که مواد نیمه پایدار نوین (مواد الهام گرفته از زمین یا طبیعت (Geo-inxpired ox bio- inspired) را ایجادکنیم؛ د) به دلیلی اهمیت توسعه تحقیقات پایهای و کاربردهای صنعتی مواد، این مقاله بر توانمندی فرآیند سولوترمال در ساخت مواد، تمرکز میکند.
مقدمه
فرایند سولوترمال را میتوان بهعنوان واکنشهای شیمیایی در محیط بسته در حضور حلال (محلول آبی یا غیر آبی) و دمای بالاتر از نقطهجوش چنین حلالی تعریف کرد. متعاقبا، فرایند سولوترمال شامل فشار بالا نیز است. دمای انتخابی (حوزه زیر یا فوق بحرانی) بستگی به واکنش مورد نیاز برای به دست آوردن ماده هدف دارد. در مورد محلولهای آبی بهعنوان حلال، فناوری هیدروترمال مورد مطالعه قرار گرفته است که منجر به توسعه اهداف مختلف زیر شده است:
الف) استخراج مواد معدنی، تحقیق روی ساخت مواد زمینشناختی؛ ب) شرایط دمایی ملایم، قادر است نفوذ شیمیایی و واکنشپذیری را بهبود بخشد تا اینکه به تهیه مواد ویژه در مرز بین مواد گوناگون از قبیل آلی/معدنی، معدنی/زیستی و غیره کمک کند؛ ج) ساخت مواد جدید؛ د) رشد بلور، بهخصوص ساخت استادانه تک بلور α-کوارتز به دلیل خواص پیزوالکتریاش؛ و) بهبود فرایند زینتر کردن تحت شرایط ملایم؛ ز) ساخت ذرات ریز با اندازه و مورفولوژیهای مختلف.
فرایندهیدروترمال-به دلیل ماهیت شیمیایی آب بهعنوان حلال – بیشتر در تهیه هیدروکسیدها، اکسی هیدروکسیدها یا اکسیدها مناسب است. توسعه مواد غیر اکسیدی (بهخصوص نیتریدها، کالگوگنیدها و غیره) نیازمند توسعه فرایندهای جدیدی است که حلالهای غیر آبی را در بر میگیرد. علاقه به مواد غیر اکسیدی منجر به توسعه واکنشهای سولوترمال برای تهیه مواد جدید یا تنظیم فرایندهای جدیدی شده است که منجر به تولید مواد نانوساختار میشود. واکنشهای شیمیایی در حلال (آبی یا غیر آبی) تحت شرایط فشار بالا و دمای ملایم (دامنه زیر یا فوق بحرانی حلال) برای توسعه شیمی و علم مواد (بهخصوص برای فناوری نانو) ظاهراً امیدوارکننده به نظر میرسد.
شاخصهای اصلی حاکم بر واکنشهای سولوترمال
دو نوع شاخص در واکنشهای سولوترمال نقش دارد:
۱ – شاخصهای شیمیایی؛ ۲ -شاخصهای دینامیکی.
جدول زیر ارتباط بین شاخصها و واکنشهای سولوترمال را نشان میدهد.
جدول ۲‑۴: شاخصهای کلیدی موثر در واکنشهای سولوترمال
شاخصهای شیمیایی
در این قسمت باید دو شاخص ماهیت واکنشگر و ماهیت حلال، در نظر گرفته شود. با کنترل غلظت پیشماده میتوان شکلهای مختلفی از ماده هدف را تهیه کرد. وانگ و همکاران با روش سولوترمال شکلهای مختلف بلور CdSe وCdTe (کروی، میلهای، غیره) را با کنترل غلظت پیشمادهها تهیه کردهاند .
انتخاب حلال نیز از طریق کنترل سازوکار واکنش میتواند نقشی کلیدی در تولید ماده هدف داشته باشد؛ بهعنوانمثال لی و همکارانش از Cu۷Te۴ با CuCl۲.H۲Oو تلوریوم بهعنوان واکنشگر، و اتیلن دی آمین بهعنوان حلال استفاده کردهاند. با استفاده از شرایط آزمایش مشابه و تغییر ماهیت حلال (بنزن و دی اتیل آمین)، تلوریوم نمیتواند با کلرید مس واکنش دهد و درنتیجه تلورید مس تولید نخواهد شد، دلیل این موضوع، میتواند مربوط به عدم قطبیت حلال بنزن باشد. علاوه بر این خاصیت کمپلکسشوندگی حلال میتواند نقش مهمی در سازوکار واکنش داشته باشد؛ مثلا تشکیل کمپلکسهای حد واسط پایدار۳(M(en یا M(en)۲ بهعنوان تمپلیت هشت وجهی و مسطح مربع میتواند مورفولوژی و ساختار محصول نهایی را تحت تأثیر قرار دهد. از این دسته، میتوان ساخت نانوساختار گل مانند ZnO را از گرماکافت کمپلکس روی-اتیلن دی آمین به کمک هگزا متیلن تترا آمین (HMTA) بهوسیله ژانگ دانگ جو مثال زد.
شکل ۲‑۲۰: ساختارهای گل مانند اکسید روی. الف) عکس با بزرگ نمایی پایین؛ ب) خوشه گلهای ZnOج) گلهایی با پدالهای چندگانه؛ د) گل مجزا با پدالهای تک لایه.
در بعضی موارد تشکیل کمپلکس-کاتیون، مرحله حد واسطه مهم در طول سازوکار واکنش سولوترمال به شمار میرود. ساخت CuInSe۲ با استفاده از InCl۳،CuCl۲ و Se در حلال اتیلن دی آمین (en) یا دی اتیل آمین در دمای ۱۸۰ درجه سانتیگراد میتواند از این دسته باشد. ساز وکار واکنش پیشنهادی شامل چهار مرحله زیر است:
حمله هستهدوستی گروه آمینی موجود در حلال، میتواند سلنیوم را به–Se۲ تبدیل کند و باعث فعال شدن Se شود؛ همچنان که سولفور نیز میتواند در محیط en به–S۲تبدیل شود.
ظاهرا تشکیل کمپلکس+ Cu(en)۲نقش مهمی در کنتزل هستهزایی و رشد نانوالیافهای تک بلور (Nano whisker) CuInSe۲دارد. با جایگزین کردن اتیلن دی آمین به اتیلن آمین بهعنوان حلال، واکنش پذیری کم میشود و مورفولوژی محصول به ذرات کروی CuInSe۲ تغییر میکند. خواص شیمی-فیزیکی حلال انتخابی، میتواند در جهتدهی ساختار فازی محصول نهایی تأثیر داشته باشد. لو و همکاران گزارش کردند که ساخت MnS در محیط حلالهای گوناگون میتواند منجر به فاز نیمه پایدار (MnS-γ-β) یا شکل پایدار (MnS-α) شود. با استفاده از ازMnCl۲.4H۲O و تیو اوره (SC(NH۲)۲) بهعنوان واکنشگر و حلال آب یا اتیلن دی آمین، ساختار پایدار (MnS-α) به دست میآید. با مواد اولیه مشابه بالا و حلال بنزن ساختار ورتزیت (MnS-γ) تهیه میشود و با تتراهیدروفوران (THF)، ساختار بلاند روی (MnS-β)مشاهده میشود. تشکیل فاز پایدار MnS-α)) حضور آب یا en میتواند مربوط به تشکیل کمپلکسر +Mn(H۲O)۶۲ یا+Mn(H۲O)۳۲ در طول واکنش باشد. اختلاف مشاهده شده بین بنزن و THF، پیشنهاد میکند که حلال غیر قطبی(C۶H۶) برای پایداری شکل ورتزیت (MnS- γ) تناسب بیشتری دارد [۶]. خواص اکسایش-کاهش محیط سولوترمال در طول واکنش میتواند با ماهیت حلال، بر محصول نهایی تأثیر بگذارد؛ مثال بارز این قسمت، تولید سولوترمال نانومیله (Sb(V)O۴ Sb(III از پودر Sb۲O۵است. در دمای مشابه ۲۰۰ درجه سانتیگراد، اگر زمان واکنش یک روز باشد؛ نانومیله Sb(III) Sb(V)O۴تشکیل میشود؛ اما بعد از سه روز فقط ذرات فلزی Sb )آنتیموان) ایجاد میشود که این مشاهده به خاصیت کاهندگی اتیلن دی آمین برمیگردد[۱۶].
ساخت نانوذرات در محیطهای غیر همگون دو فازی و یا محلولهای مخلوط همگون، نیز میتواند بر مورفولوژی محصول تأثیر بگذارد. اخیرا، گروه هانگ یو، نانوساختارهای جدید گل مانند، سیم مانند، درخت مانند CdS و CdSe را با استفاده از روش سولوترمال و کنترل نسبت دی اتیلن تری آمین ((DETA و آب دییونیزه (DIW) گزارش کردهاند[۱۷].
شاخصهای تومودینامیکی
این شاخصها عبارتند از: دما، فشار و زمان.
دما و فشار در اکثر موارد حلالیت را بهبود میبخشد. افزایش این شاخصها افزایش غلظت پیشماده را در حلال القا میکند که این خود به فرایند رشد (بهخصوص میکرو یا نانوبلورها) کمک میکند. آنالیز جزئی فاکتورهای اساسی واکنشهای سولوترمال، مشخص میکند که ماهیت حلال انتخاب شده بهخصوص در کنترل ساز و کار واکنش، نقشی کلیدی ایفا میکند.
انواع واکنشهای درگیر در فوایند سولوترمال
واکنشهای سولوترمال را میتوان به پنج دسته تقسیم کنیم:
۱) اکسایش-کاهش؛ ۲) هیدرولیز؛ ۳) گرما کافت؛ ۴) تشکیل کمپلکس؛ ۵) واکنشهای metathesis. توسعه این واکنشهای گوناگون بر کنترل دقیق شیمی حلالهای غیر آبی و به دست آوردن اطلاعات بیشتر از خواص فیزیکی-شیمیایی این حلالها اشاره دارد.
کاربردهای اصلی فرایند سولوتومال
واکنشهای سولوترمال در حوزههای گوناگون علمی توسعه داده شده است:
– ساخت مواد جدید (طراحی مواد با ساختار و خواص ویژه)؛
– تولید مواد عاملی (ظاهرشده در سنتز شیمی)؛
– رشد بلور در دمای کم (روشی برای تک بلور با حداقل چگالی نقصهای بلوری)؛
– تهیه میکرو یا نانوبلورها با اندازه و مورفولوژیهای مختلف (بهعنوان پیبش ماده سرامیکها با ساختار ریز، کاتالیزور، عناصر نانوابزارها و …)؛
– زینتر کردن در دمای پایین (تهیه سرامیکها از شکل ساختار نیمه پایدار یا مواد آمورف)؛
– ساخت لایه نازک (با توسعه فرایندهای دما پایین).
توسعه فرایندهای جدید در تهیه نانوبلورهای عاملی
در طول ۱۵ سال گذشته، دو ویژگی مهم نیرو، محرکی برای فعالیتهای تحقیقاتی شده است:
– تحقیق روی دستگاههای غیر اکسیدی به دلیل خواص فیزیکی آنها؛
– توسعه فناوری نانو و مطالعه ارتباط بین اندازه و مورفولوژی و خواص فیزیکی آنها.
در طول ۱۵ سال گذشته تحقیق روی نانوساختارهای ویژه (بهخصوص تک بعدی) مثل نانولوله، نانومیله و نانوسیم توسعه یافته است. توانمندی واکنشهای سولوترمال برای تهیه نانوساختارها بهطور ویژهای برای مواد مختلف از قبیل اکسیدها، کالگوژنیدها، نیتریدها، کاربیدها، فسفیدها، فلزات و مواد بین فلزی و … مورد تحقیق قرار گرفته است. روش سولوترمال برای نانوساختارهای اکسیدی مثل باریم تیتانات، به دلیل کاربرد در سرامیکهای دی الکتریک Fe۲O۳-α، TiO۲وA=Ca,Sr,Ba) La۱-x AxMnO۳)بهعنوان پیگمانت یا کاتالیست [۱۸]، Mn۲O۴-y Li۱-xیا LiV۲O۵-γ بهعنوان الکترود برای باتریهای لیتیومی ، PbCrO۴ و اکسیدهای مغناطیس یک بعدی برای کاربردهای نوری ، ZnO به دلیل خواص الکتریکی، نوری پیزوالکتریک استفاده میشود. روش سولوترمال برای تهیه نانوساختارهای کالگوژنید (به ویژه سولفیدها یا تلوریدها) به دلیل حیطه وسیع کاربردهای آن (بهعنوانمثال (A=Na,k)AInSe۲ Cu۲SnS۳ , ZnS,Fe1-XS, SnS NiS, CdS ) توسعه یافته است و فلوئوریدهای مختلف مثل M=Mg,Zn) KM۲+Fз یا M=Ni) سنتزشده است. نیتریدها از قبیل، CrN ،AlN،GaN،InN،ZrN،CuзN،VN به دلیل کاربردهای گوناگون آن بسیار مورد استقبال واقع شده است.
همچنین، نانومواد مختلف مثل کاربیدها : Mo۲C,B۴C، فسفیدها Ni۲P، Cu۳P، CO۲P یا TiP ؛ بوریدها TiB۲؛ با روش سولوترمال مورد تحقیق قرار گرفته است. سنتزسولوترمال نانوبلورها با مورفولوژی نانولوله در طول چند سال اخیر، بهخصوص نانولوله کربنی ، نانولوله بیسموت، نانولوله تلوریوم ، به دلیل کاربردهای ویژه این مورفولوژی توسعه داده شده است. ظاهرا واکنشهای سولوترمال روشی امیدوارکننده برای پایدارکردن کلاسترهای مولکولی جدید به شمار میرود.
نتیجه گیری
واکنشهای سولوترمال به نظر میرسد که در سنتز مواد جدید، ذرات نانوساختار، اهمیت داشته باشد. به دلیل وجود گستره وسیعی از حلالهای مختلف یا مخلوط حلالهایی که میتواند مورداستفاده قرار گیرد و واکنشهای القایی گوناگون، متناسب با طبیعت واکنشگر و ترکیب شیمیایی حلال، روش سولوترمال میتواند در توسعه فرایندهای صنعتی با شرایط دمایی و فشاری ملایم مهم باشد. به هر حال چنین توسعهای نیاز به بهبود اطلاعات ما از خواص شیمی-فیزیکی حلالهای غیر آبی تحت شرایط دما و فشارهای مختلف دارد.
کنترلر دما
کنترلر مورداستفاده در این دستگاه ،کنترلر TC4S-24R از کنترلر سری TC برند Autonics میباشد. این کنترلر ها که به آنها ترموستات نیز گفته میشود. علاوه بر نمایش دادن مقدار دما، قابلیت های دیگری نیز دارند. ترموستات ها میتوانددما یک محیط را ثابت نگه دارند. بعضی از کنترلرها می توانند بیش از یک حسگر دما را به آنها متصل کرد تا دما را نمایش دهند. توانایی خواندن و نمایش مقدار دما را PLC ها نیز دارا می باشد. اما از آنجایی که شاید از لحاظ اقتصادی در خیلی از موارد استفاده از PLC توجیح نداشته باشد از کنترلر(ترموستات) می توان بهره برد.
بعضی از کنترلرها همچنین قابلیت شبکه شدن در پروسه ی صنعتی را دارند. می توانند چندین آلارم را از آنها خواند. همچنین کنترلر عا قابلیت PID شدن را دارند که این قابلیت مهم باعث میشود که استفاده از این تجهیز راافزایش دهد.
حسگر ورودی کنترلر(ترموستاتها) معمولاً بهصورت RTD یا ترموکوپل است.
حسگر RTD :
Resistance Temperature Detectors که بهاختصار RTD نامیده میشود نوعی حسگر دمایی است که با تغییرات دما مقدار مقاومت آن تغییر میکند. در واقع مقدار دما بر اساس مقاومت حسگر تعیین میشود. یکی از پرکاربردترین سنسورهای RTD، حسگر PT100 است. در PT100 دما و مقاومت رابطه مستقیم دارند؛ یعنی با بالا رفتن دما میزان مقاومت هم افزایش مییابد و بالعکس.
ترموکوپل:
ترموکوپل “Thermocouple” از اتصال یک طرفه دو فلز غیر همجنس تولید میشود. با تغییر دما طول یکی از فلزها تغییر بیشتری نسبت به دیگری خواهد داشت که این اختلاف منجر به تولید ولتاژ بسیار ضعیفی در حد میلی ولت در طرف آزاد دو فلز میگردد. بسته به نوع فلزهای به کار رفته میتوان انواع مختلفی از ترموکوپل را ساخت. ترموکوپلها ازنظر دقت، بازه اندازهگیری دما، حساسیت و… باهم تفاوت دارند. ترموکوپل تیپ K و تیپ J از معروفترین ترموکوپلها در صنعت هستند.
انواع کنترلر دما
کنترلرهای دما بر اساس پارامترهای متفاوت به انواع مختلفی تقسیم میشود. این پارامترها شامل سایز ترموستات، نوع حسگر دمایی، نوع نصب، بازه دمایی کارکرد، روش کنترل دما، نوع خروجی ترموستات، آنالوگ یا دیجیتال بودن و … میشود.
انواع کنترلر ازنظر ظاهر
ترموستات ها در انواع تابلویی، ریلی، دیواری، داکتی و … ساخته شده و مورد بهره برداری قرار میگیرند. ترموستات تابلویی در ابعاد مختلفی ساخته میشوند که معمولاً ۴۸*۴۸، ۷۲*۷۲، ۹۶*۹۶، ۴۸*۹۶، ۹۶*۴۸ و در برخی موارد بهصورت گرد یا سایر ابعاد میباشد. این نوع ترموستاتها روی درب تابلو نصب شده و کار کنترل دما را انجام میدهند. ترموستاتهای ریلی روی ریل درون تابلو نصب میشوند. انواع دیواری و داکتی بیشتر در منازل و کاربردهای غیر صنعتی مورد بهرهبرداری قرار میگیرند.
کنترل کننده PID Controller” PID”:
کنترل کننده Proportional- Integral-Derivative controller” PID” روشی حلقه بسته (فیدبک دار) برای کنترل یک پارامتر میباشد. در این روش که معادله مشخصه آنیک معادله مرتبه ۲ از آن پارامتر میباشد با تغییر ضرایب P،I وD میتوان پاسخهای مختلفی برای نمودار آن پارامتر ایجاد کرد. سرعت پایداری، دقت پایداری و میزان اورشوت “overshoot” توسط این ضرایب تعیین میشوند. برای کنترل دما نیز از روش PID استفاده میشود. بدین صورت که دمای مورد نظر توسط اپراتور بهعنوان مرجع دما (set point) برای دستگاه تعریف میشود. سپس بسته به نوع فرایند با تعیین پارامترهای P، I و D کنترلر، دما را درآن دمای مرجع ثابت نگه میدارد. تعیین این سه پارامتر کار سخت و مبتنی بر تجربه میباشد.
معمولاً اپراتورها بهجای تعیین این ضرایب، دستگاه را در حالت اتوتیون “Auto Tune” که یک حالت از پیش تعیین شده برای این سه پارامتر است قرار میدهند. این حالت برای اکثر فرایندها مناسب میباشد و سرعت و دقت پایداری آن مناسب است. اگر اپراتور نتوانست در این مد کاری به نتیجه مطلوب برسد باید برای تنظیم این سه پارامتر به دیتاشیت دستگاه یا فرد خبره در این زمینه مراجعه کند. در برخی کنترلکنندهها بهجای استفاده از معادله مرتبه ۲ و ساخت PID controller برای کاهش هزینه فقط از معادله مرتبه ۱ استفاده میکنند. در این حالت پارامتر I یا D صفر هستند. بدین ترتیب بهجای کنترلر PID کنترلر نوع PD یا PI خواهیم داشت. در برخی موارد نیز میتوان از کنترلر نوع P استفاده کرد که عملکرد ضعیفتری نسبت به PID دارد. در سادهترین نوع کنترل کننده، از روش ON/OFF برای کنترل دما استفاده میشود.
انواع خروجی کنترلر( ترموستات):
خروجی رله:
خروجی رله در ترموستات فقط دارای دو حالت قطع و وصل (On/Off) است. در این نوع از کنترلر زمانی که دما از مقدار از پیش تعیین شده بگذرد، فرمان قطع یا وصل صادر میشود. به دلیل نوسانات دمایی و عملکرد صفر و یک بودن این ترموستات، دستگاه باید عمل قطع و وصل را بهطور مداوم انجام دهد. در برخی موارد این مسئله سبب استهلاک و کاهش عمر هیتر میشود.
خروجی SSR:
خروجی این کنترلرها بهصورت ولتاژ (ولت) است که می تواند به یک SSR با تحریک DC فرمان دهد.
خروجی آنالوگ:
خروجی در این حالت بهصورت آنالوگ میباشد که معمولاً رنج (۱۰-۰) ولت یا (۲۰-۴) میلی آمپر است. در ترموستاتهایی که خروجی آنها رله است، به دلیل قطع و وصل مکرر هیتر، تنش ایجادشده در هیتر زیاد بوده و منجر به آسیب هیتر میگردد. برای جلوگیری از ایجاد تنش در هیتر بهتر است از کنترل کننده دما با خروجی آنالوگ یا دستگاه پاور رگولاتور (کنترلر بار) استفاده کرد. بدین ترتیب بهجای خاموش و روشن شدن هیتر، توان هیتر کم و زیاد میشود تا دما در حد مورد نظر تنظیم باقی بماند.
خروجی چندگانه
در برخی ترموستاتها علاوه بر رله خروجی اصلی که بر اساس PID کنترلر است، یک یا دو رله دیگر وجود دارند که برای آلارم استفاده میشوند. همچنین برخی کنترلر ها دارای پورت ارتباطی RS485 برای ارسال اطلاعات به کامپیوتر میباشند.
کاربرد کنترلر(ترموستات):
کنترلرهادر صنایع غذایی، تزریق، ذوب فلزات، قالبریزی، پلاستیک، انواع کوره ها، صنایع شیرینی پزی، دیگ بخار، گلخانهها، موتورخانه، انواع فر ودر راکتورها بهطورکلی صنایعی که نیاز بهاندازهگیری و کنترل پارامتر دما دارد به کار میرود.
کنترلر مورداستفاده در این دستگاه ،کنترلر TC4S-24R از کنترلر سری TC برند Autonics میباشد.
مواد پیزوالکتریک
مواد هوشمند، موادی هستند که متحمل فعل و انفعالات فیزیکی میشوند. یک تعریف معادل دیگر از مواد هوشمند این است که این مواد،موادی هستند که تغییرات محیطی را دریافت کرده و با استفاده از بازخوردهای سیستم، این تغییرات را حذف یا تصحیح می کنند. مواد پیزوالکتریک، آلیاژهای حافظه دار (shape-memory alloys) ،مواد الکتروستریک( materials electrostrictive)، مواد تغییر شکل دهنده در اثر مغناطیس (magnetrostrictivematerials)، مایع های با خواص الکترورئولوژی (electrorheological fluids)، نمونههایی از مواد هوشمند متداول هستند.
تعریف و تاریخچه
پیزوالکتریسیته یک متغیر خطی است که به ساختار میکروسکوپی جامدات مربوط میشود. برخی از سرامیک ها هنگامیکه تحت تأثیر فشار قرار گیرند پلاریزه میشوند. این پدیده ی خطی و آشکار بهعنوان اثر پیزوالکتریک مستقیم The direct Piezoelectric effect) ) نسبت داده میشود. اثر پیزوالکتریک مستقیم همیشه با اثر پیزوالکتریک معکوس، همراه است. که این اثر پیزوالکتریک معکوس زمانی اتفاق می افتد که یک قطعه ی پیزوالکتریک در یک میدان الکتریکی قرار گیرد.
نواحی میکروسکوپ بوجود آمده در اثر پیزوالکتریسیته باعث جابجا شدن بارهای یونی در داخل ساختار کریستالی میشود. در غیاب نیروهای فشاری خارجی، این بارها در داخل کریستال توزیع شده و ممنتم دی پل ها همدیگر را خنثی می کنند. به هرحال، هنگامیکه یک تنش خارجی بر قطعه ی پیزوالکتریک وارد شود، بارها به گونه ای جابجا گشته که تقارن دی پل ها از میان می رود. بر این اساس یک شبکه ی پلاریزه ایجادشده و نتیجه ی آن ایجاد یک میدان الکتریکی است.
ماده ای می تواند از خود خواص پیزوالکتریک ارائه دهد که سلول واحد آن هیچگونه مرکز تعادلی نداشته باشد. خاصیت پیزوالکتریسیته به گروهی از مواد تعلق دارد که در سال ۱۸۸۰ بهوسیله پیروژاکوپ کوری در طی مطالعات آنها بر روی آثار فشار بر روی تولید بار الکتریکی در کریستال های کوارتز، کهربا و نمک راچل (Rochelle salt)، کشف شد.
در سال ۱۸۸۱ واژه ی Piezoelectricity توسط w.Hankel برای اولین بار برای نامگذاری این اثرات پیشنهاد شد. البته اثر معکوس این خاصیت توسط Lipmann از قوانین ترمودینامیک استنباط شد. در سه دهه ی بعد، همکاری های فراوانی در انجمن های علمی اروپا درزمینهٔ ی پیزو الکتریسیته انجام شد واژه ی میدان پیزو الکتریسیته بوسیله آنها استفاده شد. البته کارهای انجامشده بر روی رابطه ی میان الکترومکانیکی مختلط با کریستال های پیزوالکتریک در سال ۱۹۱۰ انجام شد و اطلاعات آن بهصورت یک مرجع استاندارد است.
به هرحال پیچیدگی علم مربوط به مواد پیزوالکتریک باعث شد که کاربردهای این مواد تا چند سال قبل رشد پیدا نکند. لانگوین ات آل در طی جنگ جهانی اول مبدل التراسونیک پیزو الکتریکی ساخت. موفقیت او باعث ایجاد موقعیت های استفاده از مواد پیزوالکتریک در کاربردهای زیر آبی شد. در سال ۱۹۳۵، Scherrer , Busch خاصیت پیزوالکتریک پتاسیم دی هیدروژن فسفات (KDP) را کشف کردند. خانواده ی پیزوالکتریک های پتاسیم دی هیدروژن فسفات اولین خانواده ی عمده از مواد پیزوالکتریک وفروالکتریک بود که کشف شده بود. در طی جنگ جهانی دوم، تحقیقات درزمینهٔ ی مواد پیزوالکتریک بوسیله ی آمریکا، شوروی سابق و ژاپن بسط داده شد. محدودیت های ساخت این مواد از تجاری شدن آنها جلوگیری می کرد اما این مسأله نیز پس از کشف باریم تیتانات و سرب زیرکونا تیتانات (PZT) در دهه های ۱۹۴۰، ۱۹۵۰ برطرف شد. این خانواده از مواد خاصیت دی الکتریک و پیزوالکتریک بسیار خوبی داشتند علاوه بر این خانواده قابلیت مناسب شدن و استفاده در کاربردهای خاص را بواسطه ی دپ کردن آنها با عناصر دیگر، دارند. تا این تاریخ، PZT یکی از مواد پیزوالکتریک پر کاربرد است.
بیشترین سرامیک های پیزوالکتریک تجاری در دسترس مانند باریم تیتانات و PZT ساختاری شبیه به ساختار پرسکیت (Perovskite) با فرمول CaTiO3 دارند. ساختار پرسکیت (ABD3) ساده ترین آرایش اتمی است که در آن اتم های اکسیژن در حالت اکتاهدرال قرار دارند و اتم های کوچکتر Nb, Sn, Zr, Ti و … بهصورت آرایش مربعی با اتم های اکسیژن پیوند خورده اند این کاتیونهای کوچکتر فضاهای اکتاهدرال مرکزی را اشغال کرده اند موقعیت های B و کاتیونهای بزرگتر Na, Ca, Sr, Ba, Pb در گوشههای سلول واحد جای میگیرند. موقعیتهای A ترکیباتی مانند KNbO3, NaNbO3, PbZro3, PbTiO3, BaTiO3 مورد مطالعه قرار گرفته و طول و دمای فروالکتریکی آنها و فازهای غیر فروالکتریک شان بهصورت وسیع استخراج شده است. این ساختارها همچنین بوسیله ی اتم های مختلف جانشین شده.تغییر میکند. تقریبا در سال ۱۹۶۵ بود که چندین شرکت ژاپنی بر روی تولید فرآیندها و کاربردهای جدید وسایل پیزوالکتریکی، متمرکز شوند. موفقیت تلاش محققین ژاپنی موجب شد تا محققین دیگر کشورها نیز به سمت تحقیقات در این زمینه جذب شوند و امروزه، نیازها و استفاده ها از این مواد در بسیاری از رشته ها ازجمله کاربردهای پزشکی، ارتباطات، کاربردهای نظامی و صنعت خودرو گسترش یافته است. بررسی تاریخچه ی پیزوالکتریسیته توسط W.G.Cady انجامشده است و در سال ۱۹۷۱ نیز کتابی با عنوان سرامیک های پیزوالکتریک منتشر شد. که این کتاب هنوز هم بهعنوآنیکی از منابع قوی درزمینهٔ ی پیزوالکتریک ها مطرح است.
فرآیند تولید سرامیک های پیزوالکتریک
تولید اغلب سرامیک های پیزوالکتریک توده ای با تهیه ی پودر آنها شروع میشود. پودر تولیدی سپس در اندازه و شکل مورد دلخواه پرس میشود. شکل خام تولیدی خشک و فرآوری گشته و از لحاظ مکانیکی سخت تر و پر دانسیته تر میشود. مهمترین فرآیندهایی که بر روی خواص و ویژگی های محصول تولیدی اثر می گذارند شامل: فرایند تولید پودر، فرآیند خشک کردن پودر و زینترینگ می باشد. مراحل بعدی انجامشده شامل: ماشین کاری، الکترونیک و قطب دار کردن (Poling) میشوند قطب دار کردن یعنی: استفاده از یک میدان DC جریان برای جهت دهی به دی پل ها و القای خاصیت پیزوالکتریکی است. معمولی ترین روش برای تهیه ی پودر، مخلوط کردن اکسیدهای مورد نیازاست. در این فرآیند، پودر از مخلوط کردن نسبت های استوکیومتری مناسب از اکسیدهای تشکیل دهنده ی
برای نمونه برای تولید (Lead Zirconiate titanate) PZT ، اکسید سرب، اکسید تیتانیم و اکسید زیرکونیم، ترکیبات اصلی هستند. براساس کاربرد و استفاده ای که از پیزو الکتریک تولیدی میشود، انواع متنوعی از عناصر دوپ شونده نیز به مخلوط افزوده میشود. که این عناصر دوپ شده موجب ایجاد خواص مورد نظر ما میشوند. سرامیک های PZT به ندرت بدون استفاده از افزودنی های دوپ شونده تولید میشوند. استفاده از عناصر دوپ شونده موجب اصلاح برخی از خواص این نوع سرامیک ها میشوند. افزودنی های دوپ شونده ای که در موقعیت های A قرار می گیرند باعث کاهش ضریب اتلاف (dissipation factor) شده که این مسأله بر روی تولید گرما تأثیر می گذارد، اما باعث کاهش ضرایب پیزوالکتریسیته (Piezoelectric coefficients) میشود. به همین دلیل پیزوالکتریک های تولیدی با این افزودنی ها بیشتر در کاربردهای التراسونیک و با فرکانس بالا استفاده میشوند. افزودنی های دوپ شونده ای که در موقعیت های B قرار می گیرند، باعث افزایش ضرایب پیزوالکتریسیته میشوند اما همچنین موجب افزایش ثابت دی الکتریک شده که این مسأله زیان آور است. پیزوالکتریک های تولیدی با این افزودنی ها دوپ شونده، بهعنوان فعال کننده در کنترل کننده صدا- لرزش (control vibration and noise) ، عضله های خم کننده (benders)، کاربردهای موقعیت یابی نوری (optical positioning application) و … استفاده میشوند.
مخلوط نمودن پودر اکسیدهای مورداستفاده در تولید سرامیک های پیزوالکتریک یک به دو روش انجام میشود که در زیر بیان شدهاند
- روش سایش خشک با بال میل
- روش سایش تر با بال میل
هر دو روش تر و خشک دارای مزایا و معایبی هستند. روش سایش تر با بال میل سریع تر از روش خشک است. به هر حال عیب روش تر اضافه شدن مرحله ای برای جداسازی مایع از پودر تولیدی است. متداول ترین روش تولید PZT ها از سایش تر با بال میل بهره میگیرد. در روش سایش تر پودر پودر این سرامیک ها با بال میل، از اتانول بهعنوان مایع و از زیرکونیای تکلیس شده بهعنوان محیط سایش استفاده میشود. البته ممکن است بهجای یک آسیاب معمولی از یک آسیاب ارتعاشی (Vibratory mill) استفاده شود. این فرآیند که توسط Herner ابداع شده خطر آلودگی پودر با اجزای جدا شده از گلوله ها و محیط سایش را کاهش می دهد همچنین محیط زیرکونیا به خاطر کاهش ریسک آلودگی استفاده میشود.البته مرحله ی تکلیس نیز یکی از مراحل تعیین کننده در تولید سرامیک های PZT است. این مرحله موجب کامل شدن فرآیند تبلور کشته که فاز پرسکیت در این مرحله تشکیل میشود. اهداف این مرحله خارج شدن مواد آلی و فرار از مخلوط است و واکنش اکسیدهای موجود در مخلوط برای ایجاد ترکیبات فازی مناسب قبل از فرآیند تولید قطعه است. همچنین از اهداف دیگر این مرحله کاهش حجم شرپنکیج و یکنواختی بهتر در طی زینترینگ و پس از آن است. پس از تکلیس، یک ماده ی چسبنده به پودر افزوده میشود و مخلوط شکل دهی میشود. شکل دهی قطعات ساده با روش پرس خشک در قالب و برای بدنه های پیچیده تر، روشهای اکستروژن و ریخته گری دوغابی استفاده میشود. پس از آن اشکال تولیدی زینترینگ میشود. مشکل عمده در زینترینگ سرامیک های PZT، فراریت Pbo در دمای ۸۰۰ درجه سانتی پایه است برای به حداقل رساندن این مشکل، نمونههای PZT در حضور یک منبع سرب مانند PbZro3 زینتر میشوند و در داخل یک بوته ی ذوب بسته حرارت دهی میشوند. اشباع شدن اتمسفر محل زینتر کردن با PbO باعث به حداقل رسیدن اتلاف سرب از بدنه های PZT میشود. در این شرایط زینترینگ می تواند در دمای متنوعی بین ۱۲۰۰-۱۳۰۰ درجه سانتیگراد انجام شود. با وجود این تدابیر پیش بینی شده معمولاً اتلاف ۲-۳% در مقدار سرب اولیه صورت میگیرد. پس از برش و ماشین کاری قطعه به شکل مناسب، الکترودها تعبیه میشود و یک میدان DC برای جهت دهی به قلمرو دی پل های داخل سرامیک پلی کریستال اعمال میشود. قطب دار کردن بوسیله ی جریان DC می تواند در دمای اتاق و یا در دماهای بالاتر انجام شود. البته این مسأله به ماده و ترکیب سرامیک بستگی دارد. فرایند پلاریزاسیون تنها اندکی دی پل های موجود در سرامیک پلی کریستال را هم جهت می کند و نتیجه ی پلاریزاسیون پلی کریستال کمتر از حالتی است که سرامیک تک کریستال باشد. این تکنیک تولید دارای ابهامات زیادی است البته تعداد زیادی از روشهای تولید دیگر وجود دارد که سرامیک های PZT با خواص و ریزساختار عالی تولید می کنند. یک مشکل بوجود آمده در این روش انحراف از حالت استوکیومتری است. این مشکل اغلب به خاطر وجود ناخالصی در مواد اولیه و اتلاف سرب از بدنه در طی فرآیند زینترینگ بوجود می آید. که باعث تغییر خواص PZT در اثر جانشینی های ناخواسته، میشود. بهعنوآنیک نتیجه، خواص الاستیک در اثر این مشکل می تواند ۵% ، خواص پیزوالکتریک ۱۰% و خواص دیک الکتریک ۲۰ درصد تغییر میکند. همچنین، خواص دی الکتریک و پیزوالکتریک عمدتاً به علت عدم وجود یکنواختی کاهش پیدا می کنند (این عدم یکنواختی به خاطر هم زدن کم اتفاق می افتد). این مسأله هنگامیکه اکسیدهای اصلی هم گون باشد مهم می باشد. در روشهای توضیح داده شده در بالا، به هرحال، اجزای اصلی بهصورت محلول جامد در آمده و این نشان داده شده است که مخلوط شدن هم گون محلول جامد هنگامیکه این مسأله امکان نداشته باشد، مشکل است.
روابط ساختاری و خواص مواد
دانستن اطلاعات مربوط به پیزوالکتریسیته از ساختار مواد شروع میشود. برای توضیح بهتر، بر روی یک کریستال کوچک با قطر میانگین کمتر از Mm100 یک سرامیک پلی کریستال متمرکز شویم. این کریستال از اتم های مثبت و منفی تشکیلشده است که فضای خاصی را در سلولهای تکراری (سلول واحد) اشغال کرده اند. تقارن خاص سلول واحد تعیین کننده ی این مسأله است که آیا کریستال ما خاصیت پیزوالکتریسیته دارد یا نه؟ همه ی کریستال ها از ۳۲ کلاس از ۷ سیستم: (تریکلینیک، مونوکلینیک، ارتورومبیک، تتراگونال، رمبوهدرال، هگزاگونال و کیوبیک) مشتق شدهاند. از ۳۲ کلاس، ۲۱ عدد از آنها دارای تقارن مرکزی نیستند و ۲۰ کلاس دارای خواص پیزوالکتریک هستند. یک کلاس از ۲۱ کلاس فاقد تقارن مرکزی، پیزوالکتریک نیست زیرا این کلاس دارای دیگر عناصر تقارن است). نبودن مرکز تقارن بدین معناست که یک حرکت شبکه ی یونهای مثبت و منفی نسبت به همدیگر که درنتیجه ی اعمال تنش بوجود می آید،تولید یک دو قطبی الکتریکی می کند. یک سرامیک از قرارگیری تصادفی این کریستال های پیزوالکتریک تشکیلشده است و به همین دلیل غیرفعال است. اثرات کریستال ها همدیگر را خنثی نموده و خاصیت پیزوالکتریک قابل اندازه گیری در سرامیک بوجود نمی آید. نواحی با بردار قطبی یکسان،قلمرو (domain) نامیده میشوند.
قطب دار کردن یکی از روشهای معمولی مورداستفاده برای جهت دهی به قلمرو هاست که این عمل بوسیلهی پلاریزاسیون سرامیک ها با استفاده از یک میدان الکتریکی ساکن انجام میشود. الکترودها بر روی سرامیک اعمال میشود تا قلمروهای پیزوالکتریکی چرخیده و در جهت میدان،جهت گیری کنند. نتیجه ی بهدستآمده اینگونه نیست که تمام قلمروها هم جهت شوند و با جهت گیری یکسان بخشی از قلمروها سرامیک پلی کریستال دارای یک اثر پیزوالکتریکی بزرگ میشود. در طی این فرایند ماده ی پیزوالکتریک در جهت محور قطبی شدن انبساط و در جهت عمود بر آن انقباض دارد.
کاربرد مواد پیزوالکتریک
مواد پیزوالکتریک کاربرد وسیعی در علوم مختلف دارند. این مواد در بسیاری از وسایل که نیازمند تغییر انرژی مکانیکی به الکتریکی و یا بالعکس است، استفاده میشوند. زمینه ی وسیعی از کاربردهای مواد پیزوالکتریک وجود دارد و با وجود این مسأله که این مواد نزدیک به یک قرن است که مورد مطالعه قرار گرفته اند. ولی هنوز هم پتانسیل استفاده شدن در کاربردها و ابداعات دیگر را دارند. در سالهای اخیر پیزوالکتریک ها کاربردهای فراوان و حساسی ازجمله حسگرهای پیزوالکتریکی در صنعت خودرو، تستهای غیرمخرب ،مراقبت های پزشکی، در فرهای مایکروویو و در یخچال ها. بعلاوه از آنها در اتمایزرها، آژیرهای خطر، و همچنین یک استفاده مهم سرامیک پیزوالکتریک ، عمق یابی در دریا تا تجهیزات ردیاب زیردریایی ها است ؛ جدیدترین کاربردهای این مواد، در پرینترهای سه بعدی است . از مواد فعال کننده نویز تا ایستگاه های فضایی، پیزوسرامیک ها اجزای کلیدی مورد نیاز برای ساخت قطعات پیشرفته و سیستمهای کارآمد را تشکیل خواهند داد.
۳- فصل سوم : نحوه ساخت و طراحی
چندین نوع راکتور هیدروترمال در واکنشهای شیمیایی مورداستفاده قرار میگیرد که در زیر به آنها اشاره میکنیم :
- راکتور هیدروترمال ss با شل داخلی PTFE
- راکتور هیدروترمال ss یا شل داخلی PPP
- راکتور هیدروترمال ss بدون شل داخلی
- راکتور هیدروترمال ss با شل داخلی PTFE و سیستم حرارت دهی و کنترل دما
- راکتور هیدروترمال ss یا شل داخلی PPP و سیستم حرارت دهی و کنترل دما
- راکتور هیدروترمال ss بدون شل داخلی و سیستم حرارت دهی و کنترل دما
- راکتور هیدروترمال ss با شل داخلی PTFE و سیستم حرارت دهی و کنترل دما و کنترل فشار
- راکتور هیدروترمال ss یا شل داخلی PPP و سیستم حرارت دهی و کنترل دما و کنترل فشار
- راکتور هیدروترمال ss بدون شل داخلی و سیستم حرارت دهی و کنترل دما و کنترل فشار
تمامی راکتورهای بالا با بدنه تیتانیومی نیز ساخته میشوند. در حالت کلی چندین نوع مواد اولیه برای شل بیرونی راکتور مورداستفاده قرار میگیرد که عبارتاند از استیل ۴۲۰ ، استیل ۳۰۴ و استیل ۳۱۶ ، تیتانیوم. که در این بین بهترین سیستم برای راکتورها برای سنتز نانومواد با خاصیت مغناطیسی همان استیل ۳۱۶ می باشد. تقلن داخلی از جنس PTFE نهایتا تا دمای ۲۸۰ درجه در برابر دما مقاوم است و PPP تا دمای ۳۵۰ درجه در برابر حرارت مقاوم است. جهت دسایابی به دمای بالاتر جهت سنتزهای خاص باید تفلن داخلی حذف شود و خود بدنه آب بندی گردد. در زیر تصاویر از انواع راکتورها را مشاهده می کنید.
شکل ۳‑۱ : راکتور هیدروترمال با بدنه استیل مقاوم تا دمای ۲۸۰ درجه سانتی پایه و شل داخلی PTFE
شکل ۳‑۲: کوره ی افقی جهت قرار گیری راکتورهای هیدروترمال بدون سیستم گرمایشی
شکل ۳‑۳: سیستم کنترل دما همراه باهمزن مغناطیسی برای راکتورهای هیدروترمال
شکل ۳‑۴: محفظه ضد انفجار برای راکتورهای هیدروترمال با فشار بالا
شکل ۳‑۵: راکتور هیدروترمال دارای فشارسنج آنالوگ
شکل ۳‑۶:راکتور هیدروترمال با سیستم کنترل دما و فشار و کوره مخصوص جهت گرامادهی
شکل ۳‑۷:نمایی از راکتور هیدروترمال بدون شل داخلی PTFE
شکل ۳‑۸ : نمایی از راکتور هیدروترمال با شل داخلی ppp مقاوم تا ۳۵۰ درجه سانتی پایه
شکل ۳‑۹: معرفی قسمت های مختلف از راکتور هیدروترمال
مزیت های راکتور طراحی شده :
- محدوده ی دمایی ۲۰۰- تا ۳۵۰ درجه سانتی پایه
- پخش یکنواخت دما
- ضد خاصیت مغناطیسی جهت انجام واکنشهای خاص
- سرعت انتقال دما تا ۵ درجه سانتی پایه بر دقیقه
- ساختار منطقی ، بدون مواد سازنده خطرناک ، بدون آلودگی محیط زیست با تضمین ایمنی
- بدنه استیل ضد زنگ ، ضد اسید ، ضد خوردگی ، بدون خاصیت مغناطیسی
- بدنه داخلی PTFE و PPP ، ضد زنگ ، ضد اسید ، ضد باز ، ضد مواد شیمیایی ، ضد خوردگی و از سه جنس PTFE ساده ، گرافیتی و برنزی
- طول عمر بسیار بالا ، قیمت پایین
- عدم وجود نمونه داخلی
مزیت نسبت به نمونه خارجی
- قیمت پایین تر نسبت به نمونه خارجی (کمتر از یک چهارم)| ارزآوری مستقیم
- پخش یکنواخت دما
- دارا بودن سه نوع شل داخلی برای واکنشهای مختلف
- دما و فشار کاری بالاتر (دمای ۳۶۰ درجه و فشار ۵۰ مگا پاسگال)
- قابلیت طراحی در همه ابعاد ، همه حجم ها متناسب با نیاز های داخلی
در زیر قیمت نمونههای خارجی و نمونه تولیدی ما را مشاهده می نمایید:
نام محصول | قیمت نمونه خارجی (یورو) | قیمت فروش شرکت |
راکتور هیدروترمال ۵۰ میلی لیتر | ۴۰۰ یورو | |
راکتور هیدروترمال ۱۰۰ میلی لیتر | ۷۰۰ یورو | |
راکتور هیدروترمال ۲۰۰ میلی لیتر | ۱۰۰۰ یورو | |
راکتور هیدروترمال ۱۰۰ میلی لیتر با کنترال دما و فشار ، سرامیکی | ۹۰۰۰۰ یورو |
مشخصات راکتور تولیدی
- ویژگی ها :
- محدوده ی دمایی ۲۰۰- تا ۳۸۰ درجه سانتی پایه
- دارای سیستم رابط بین هیتر و راکتور جهت افزایش و کاهش کنترل شده دما | تا ۰.۱ درجه سانتی پایه
- اتصال مستقیم حسگر دما به راکتور و یا رابط بین هیتر و راکتور برای افزایش دقت و کنترل در دما
- امکان اتصال همزمان چند راکتور به یک سیستم کنترل جهت افزایش واکنشهای همزمان
- دقت سیستم کنترلی تا ۰.۱ درجه تا دمای ۱۰۰ و ۱ درجه تا دمای ۳۸۰ درجه سانتی پایه
- پخش یکنواخت دما
- دارای سیستم همزن دار مغناطیسی همراه با سیستم کنترل جهت تنظیم سرعت
- ضد خاصیت مغناطیسی جهت انجام واکنشهای خاص
- سرعت انتقال دما تا ۰.۱ درجه سانتی پایه بر دقیقه تا دمای ۱۰۰ و ۱ درجه تا دمای ۳۸۰ درجه سانیت پایه
- ساختار منطقی ، بدون مواد سازنده خطرناک ، بدون آلودگی محیط زیست با تضمین ایمنی همراه با محفظه ضد انفجار
- بدنه استیل ضد زنگ ، ضد اسید ، ضد خوردگی ، بدون خاصیت مغناطیسی
- بدنه داخلی PTFE و PPP ، ضد زنگ ، ضد اسید ، ضد باز ، ضد مواد شیمیایی ، ضد خوردگی و از سه جنس PTFE ساده ، گرافیتی و برنزی
- طول عمر بسیار بالا ، قیمت پایین |
- سیستم کنترلی بهصورت سوکت طراحی شده و قابلیت کوپل شدن با سایر سیستم ها و همچنین قابلیت استفاده مستقل را داراست.
- عدم وجود نمونه داخلی | عدم وجود نمونه خارجی مشابه (نمونه خارجی سیستم همزن ندارد)
مزیت نمونه تولیدی ما نسبت به نمونه خارجی:
- مزیت نسبت به نمونه خارجی :
- دارای سیستم رابط بین هیتر و راکتور جهت افزایش و کاهش کنترل شده دما | تا ۰.۱ درجه سانتی پایه ، در نمونه خارجی وجود ندارد.
- اتصال مستقیم حسگر دما به راکتور و یا رابط بین هیتر و راکتور برای افزایش دقت و کنترل در دما | نمونه خارجی حسگر به هیتر متصل است.
- امکان اتصال همزمان چند راکتور به یک سیستم کنترل جهت افزایش واکنشهای همزمان| نمونه خارجی تنها یک راکتور قابلیت اتصال دارد.
- دارای سیستم همزن دار مغناطیسی | نمونه خارجی سیستم همزن ندارد.
- لایه واسط از جنس آلیاژ های خاص جهت کنترل بیشتر بر روی سرعت گرم و سرد شده راکتور
- سیستم کنترلی بهصورت سوکت طراحی شده و قابلیت کوپل شدن با سایر سیستم ها و همچنین قابلیت استفاده مستقل را داراست
- قیمت تمام شده بسیار پایین تر نسبت به نمونه خارجی | ارز آوری مستقیم
شکل ۳‑۱۰: راکتور هیدرومال تولیدی با کنترل دما
شکل ۳‑۱۱:معرفی قسمت های مختلف راکتورهای هیدروترمال دارای کنترل دما و فشار باقابلیت اتصال به کامیوتر
شکل ۳‑۱۲: نمونه ای از راکتور هیدروترمال غیر استاندارد منفجر شده
شکل ۳‑۱۳: نمونه ای از کوره ای که یک عدد راکتور هیدروترمال غیر استاندارد و بی کیفیت در آن منفجر شده است
در ادامه جدول مقاومت انواع پیشماده ها جهت ساخت راکتور نسبت به مواد شیمایی مختلف نشان داده شده است:
جدول ۳‑۱: جدول مقاومت انواع پیشماده ها جهت ساخت راکتور نسبت به مواد شیمایی مختلف
۰ دیدگاه دربارهٔ «راکتور هیدروترمال»
امتیاز بینندگان:۵ ستاره